【製品】 from STAFF職人を訪ねて Vol.2
Gear企画開発課Kayo Mizutani/水谷 佳世
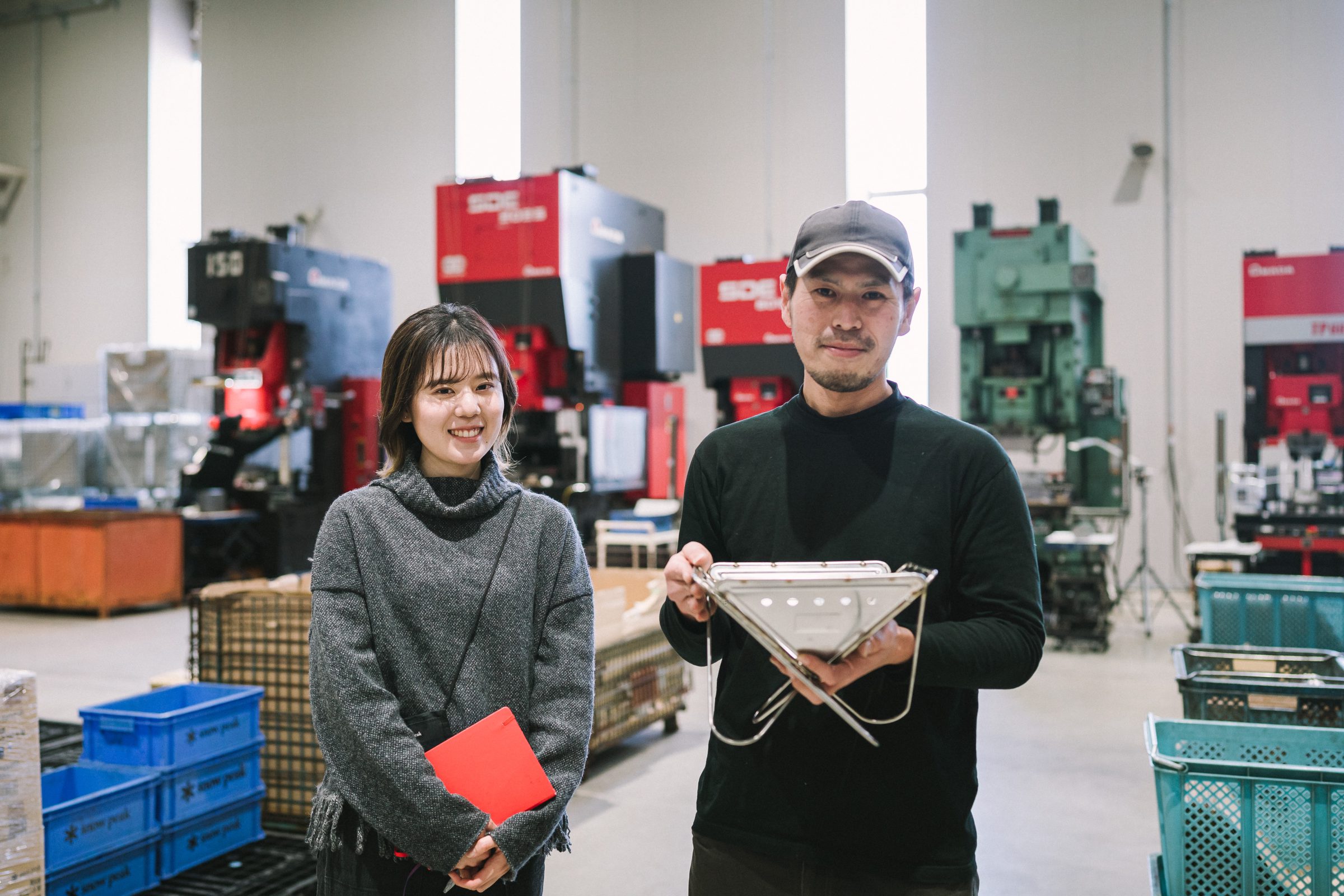
Prologue
燕三条が誇る金属加工の工場をはじめ、全国・世界各地のパートナー工場でつくられるスノーピーク製品。それらは、機械と職人の知見や技術を組み合わせることで生み出されます。
そんな製品群が工場でどのようにつくられているのか、スタッフが詳しくご紹介します。
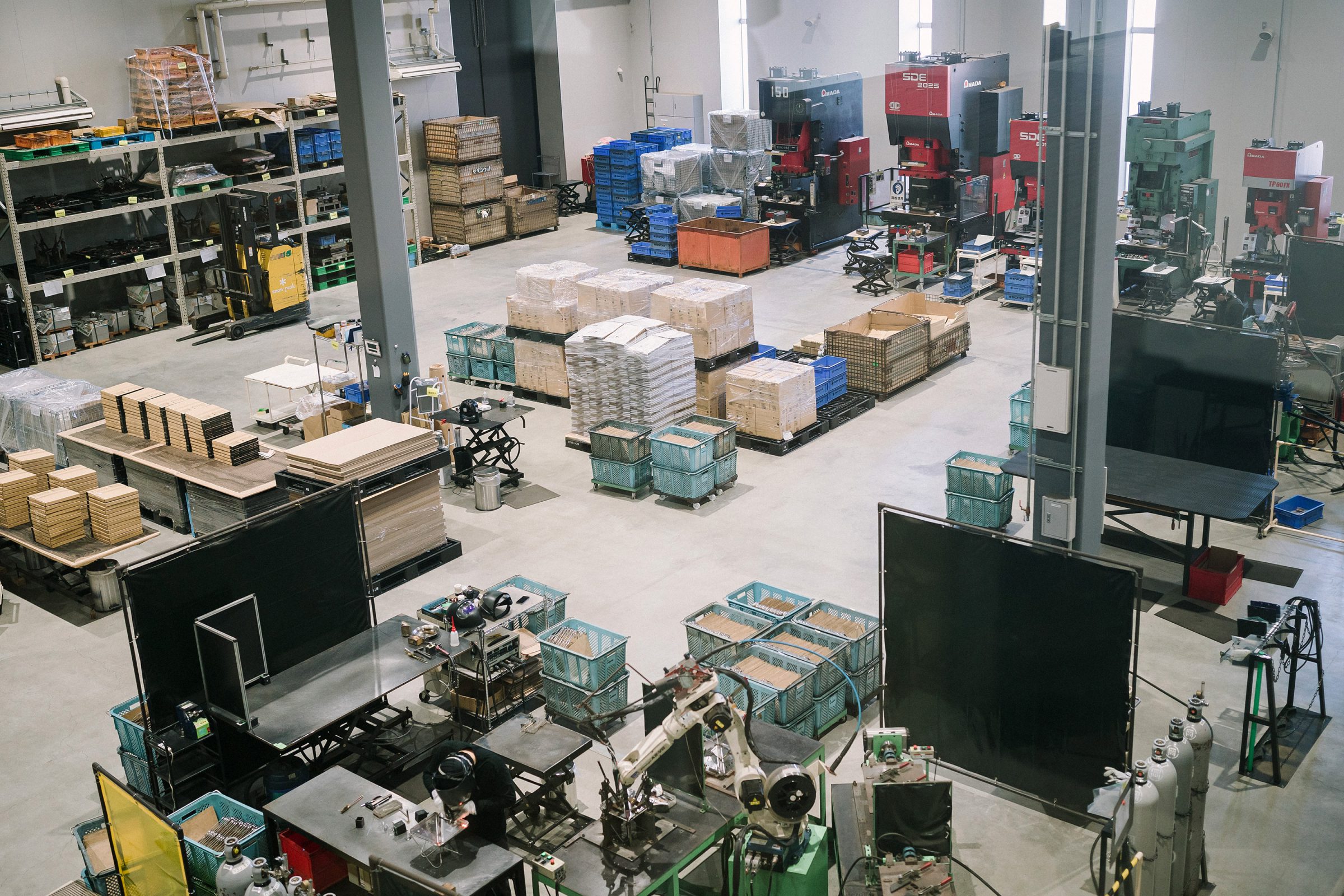
写真左奥にあるのがプレス機。手前には溶接、梱包スペースがある。
今回紹介するのは、Snow Peak Operation Core HQ2(以下HQ2)内にある、焚火台の工場。
その製造の模様を、開発スタッフの水谷がリポートします。
◇焚火台という新たな概念の誕生
スノーピークの代名詞的な存在でもある焚火台。工場をご案内する前に、まずはその誕生の物語についてご紹介します。
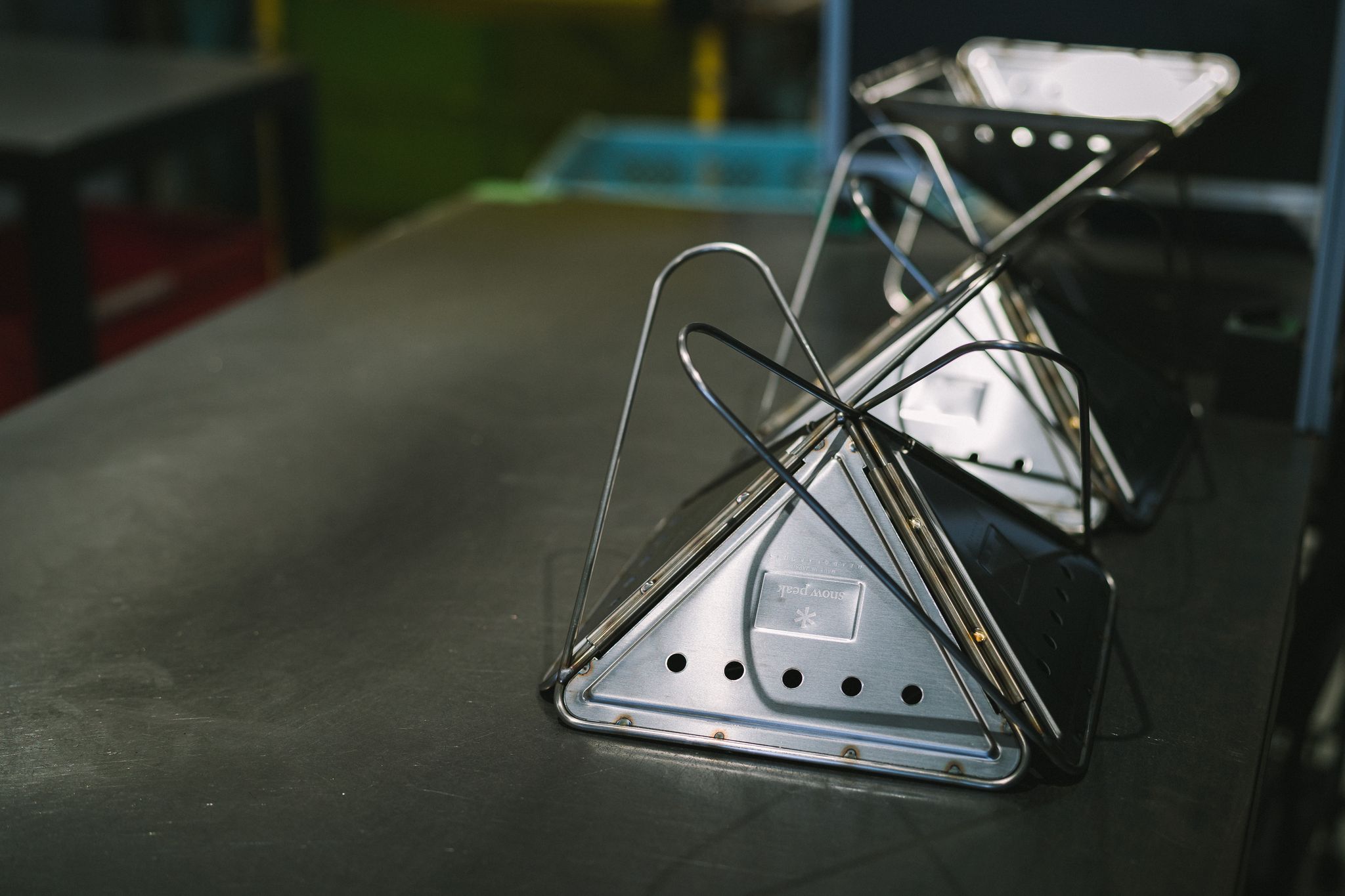
焚火台を発売したのは1996年。開発のきっかけは、当時のキャンパーのマナーが原因でした。
1990年代は地面むき出しのキャンプ場が多く、焚火は直火で楽しむことが常識とされていましたが、オートキャンプブームにより芝が整えられた直火禁止のキャンプ場が数多く新設されていきました。
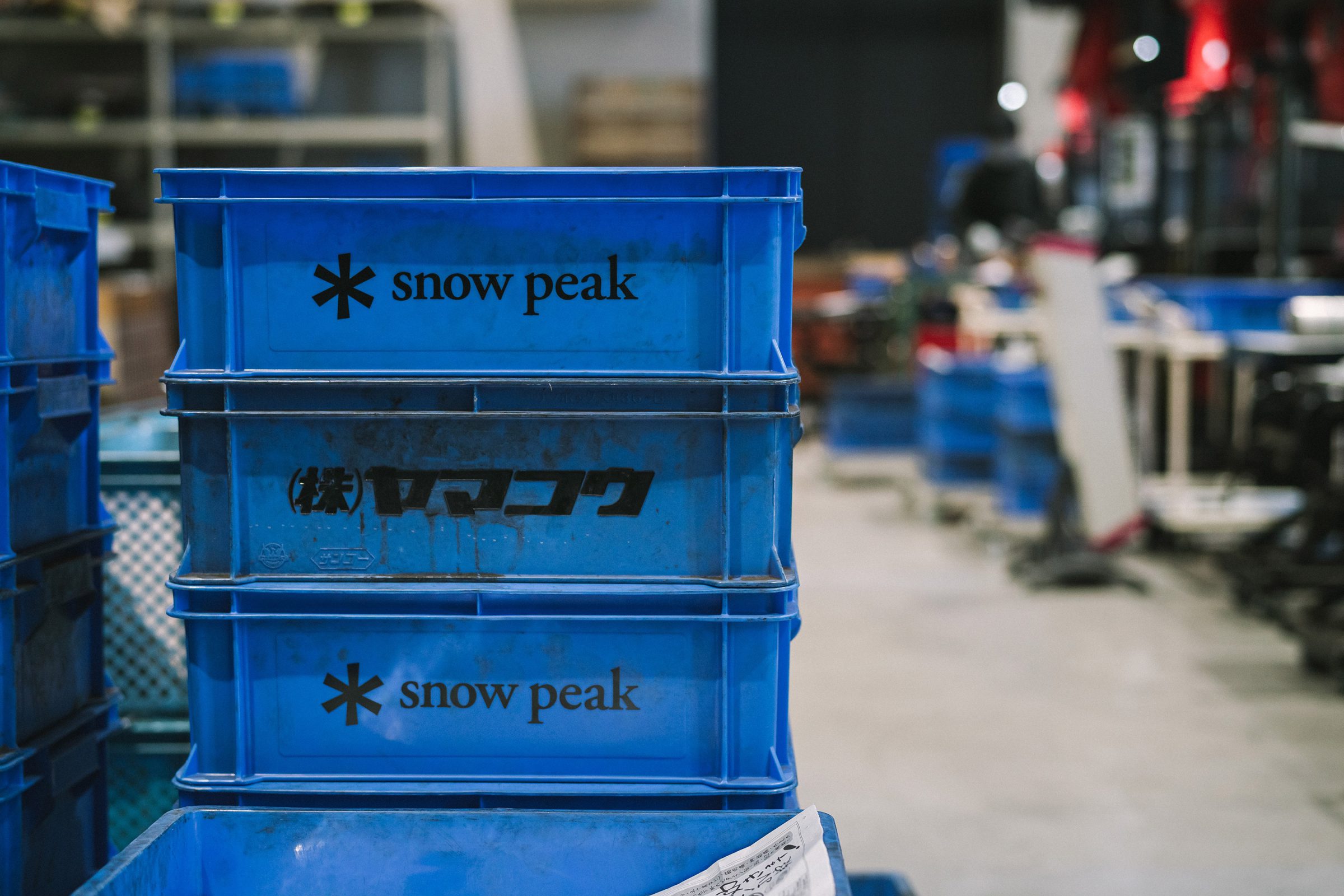
焚火台発売年に社名変更。当時のボックスはいまも現役。
それでも、ルールを守らずに直火で焚火を楽しむキャンパーが後を絶たず、サイトには黒く焼け残った無残な跡が多く残ったのです。
そのことに心を痛めたスタッフが開発したのが、焚火を楽しむための「焚火台」です。
「自然にダメージを与えずに焚火を楽しむ」というスノーピークの提案は、時間をかけてユーザーの口コミとともに広がり、キャンパーのルールから、やがて常識のマナーへと定着していきました。
今はあらゆるブランドから発売されている焚火台ですが、実はそんな歴史があるのでした。
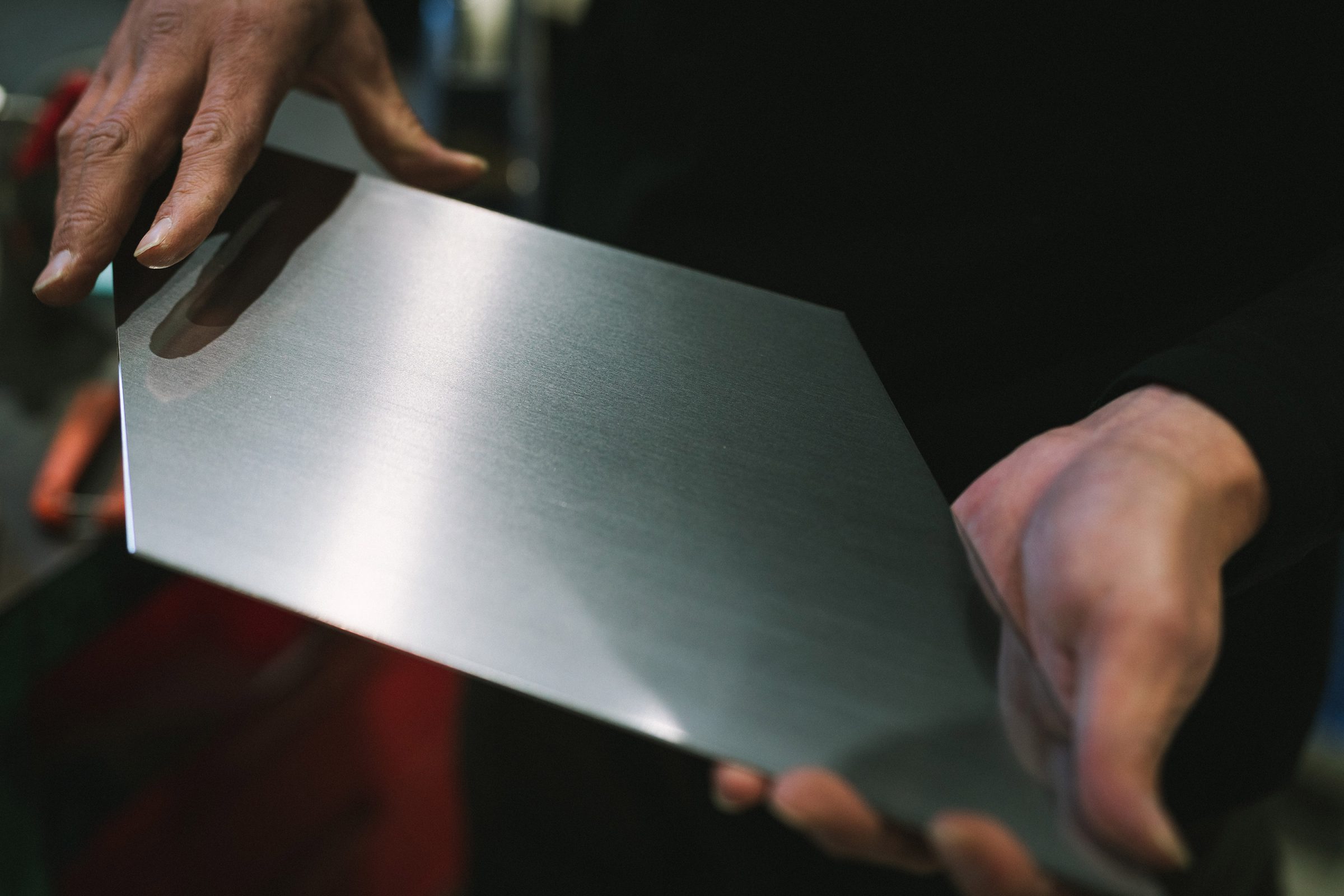
Step 1
縁取りとロゴを刻印。
それでは、製造工程を追っていきましょう。まず最初に菱形のステンレスの材料をプレスして三角形の縁を作り、同時にスノーピークのロゴを刻印します。
「ロゴの下にあるHEADQUATERSという文字は、この自社工場で作っていることを示す証です」。そう話すのは、良品製造課マネージャーの小林です。
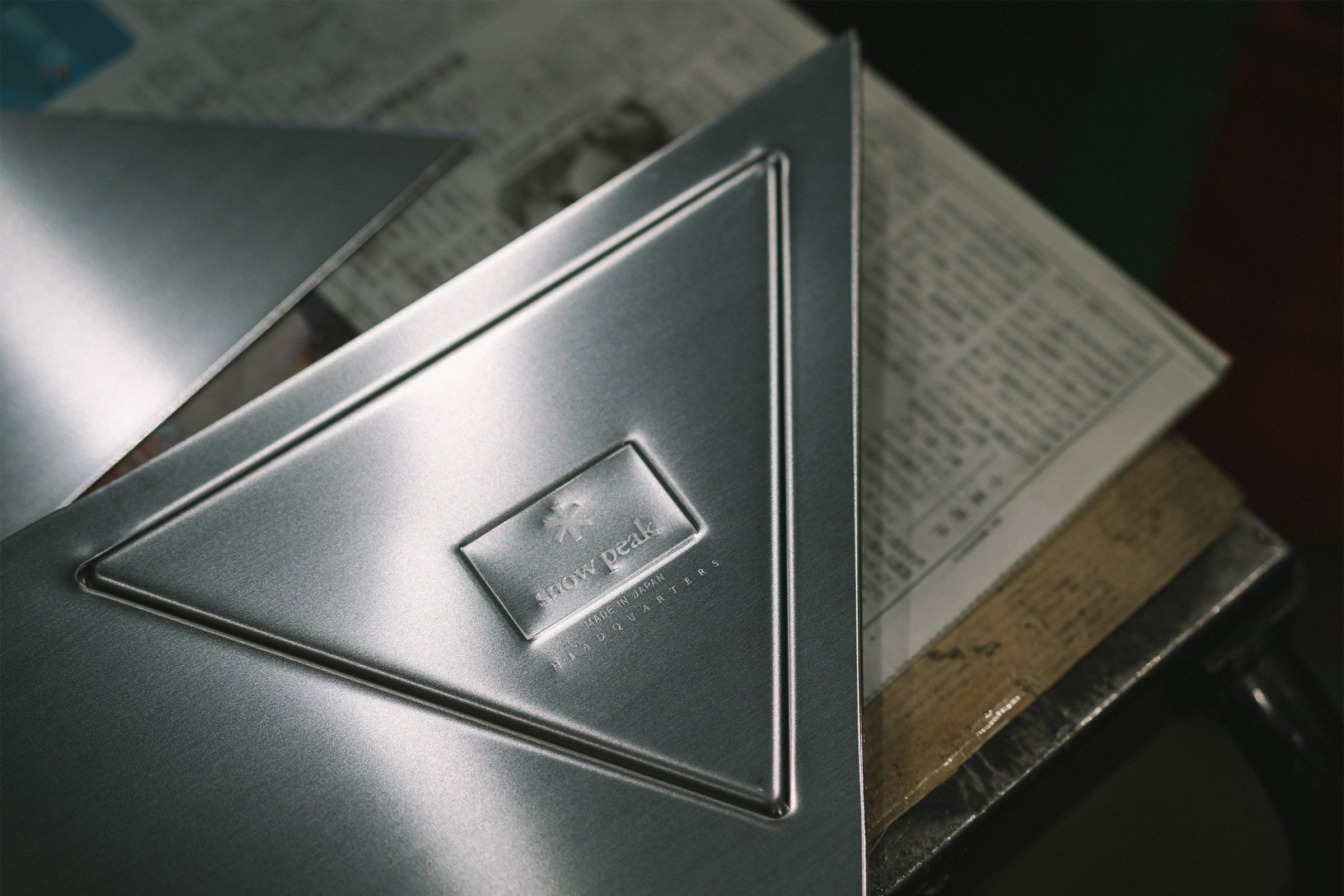
プレスによってロゴが刻まれる。
スノーピークでは、2011年の本社移転を機に、自社工場での焚火台の製造を開始しました。
その後、年々高まる国内外の需要に応えるべく、2020年からはLサイズの焚火台を社外の協力工場に製造移管し、現在はSとMサイズを自社工場で製造しています。
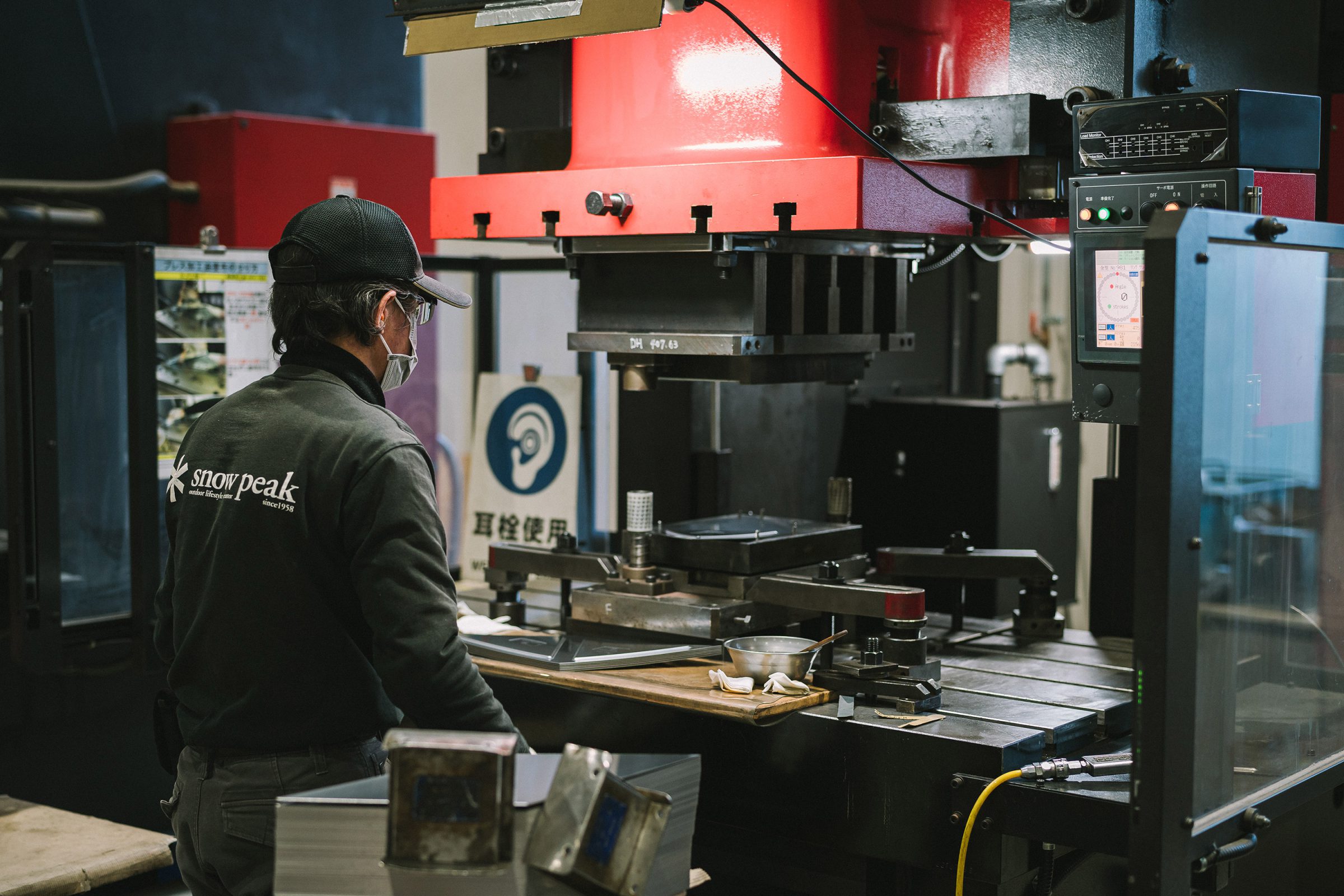
プレス機の大きな音が工場内に響き渡る。
Step 2
プレスで三角形に抜き出す。
最初のプレスでの成形が終わったら、すぐ隣にある別のプレス機で空気を取り入れるための穴を開け、側面の成形を行います。そして、そこから三角形のステンレス板を2枚取り出します。
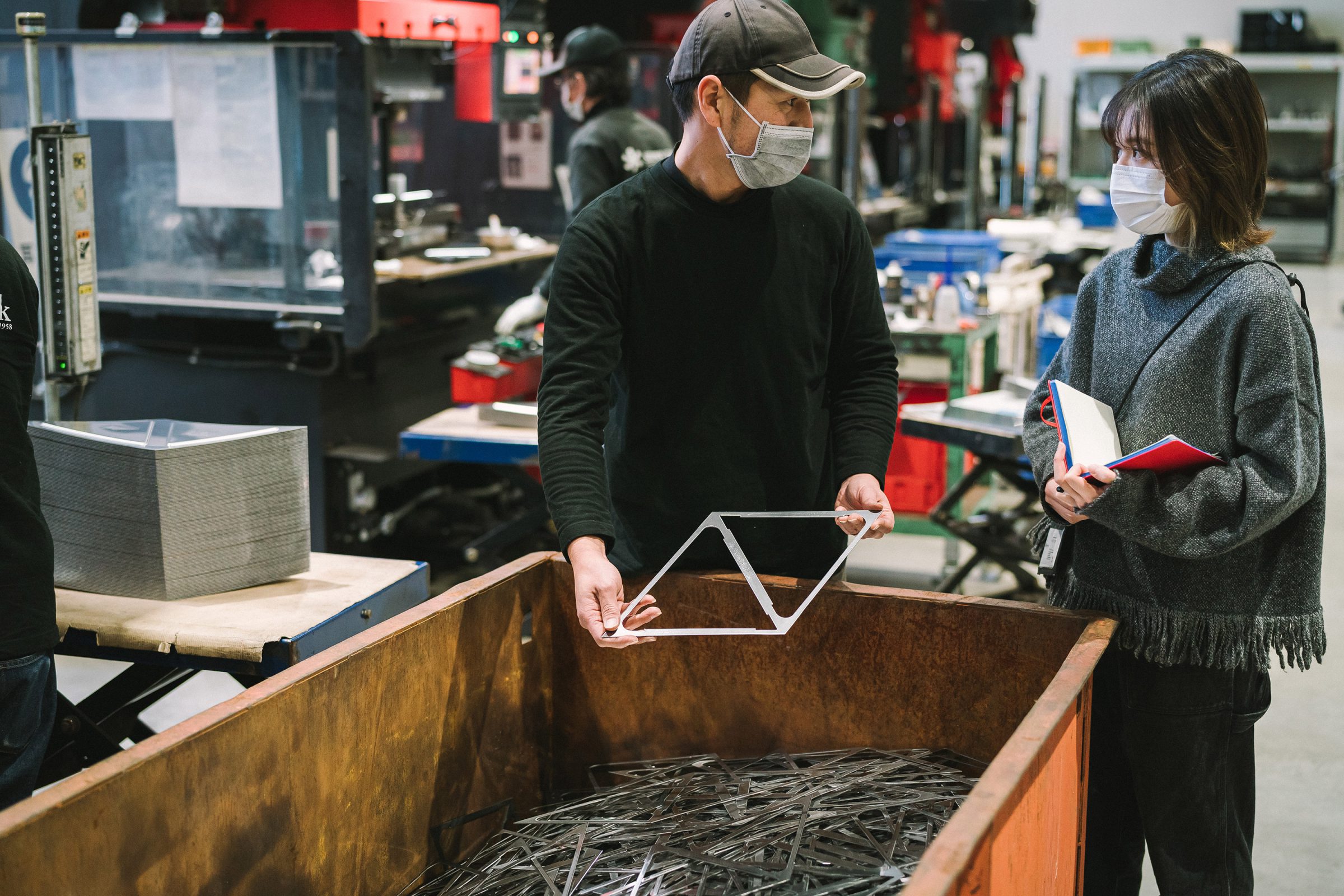
コンテナの中には端材が貯められている。写真左が良品製造課の小林。
「残ったステンレスの端材は溶かして再度活用しています」と小林。
私は大学時代、デザインを学びながら環境問題にも注目し、地球環境への負荷を抑えたものづくりを目指す必要があると考えていました。このような端材の再利用の仕組みを知り、とても安心しました。
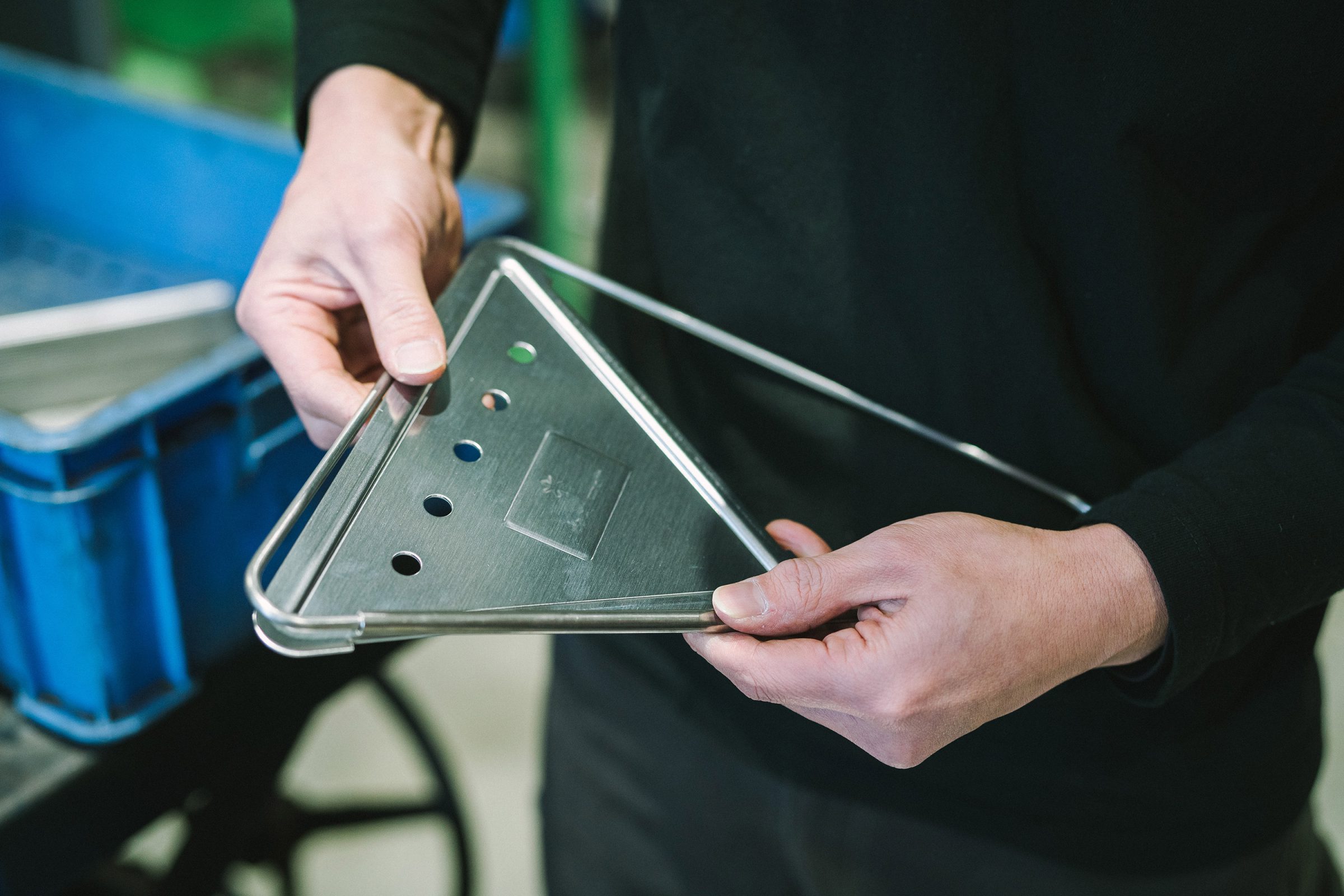
Step 3
パイプとステンレス板を溶接。
三角形のステンレス板は、次に溶接スペースへ。パイプを組み合わせ、ロボットで溶接を行います。
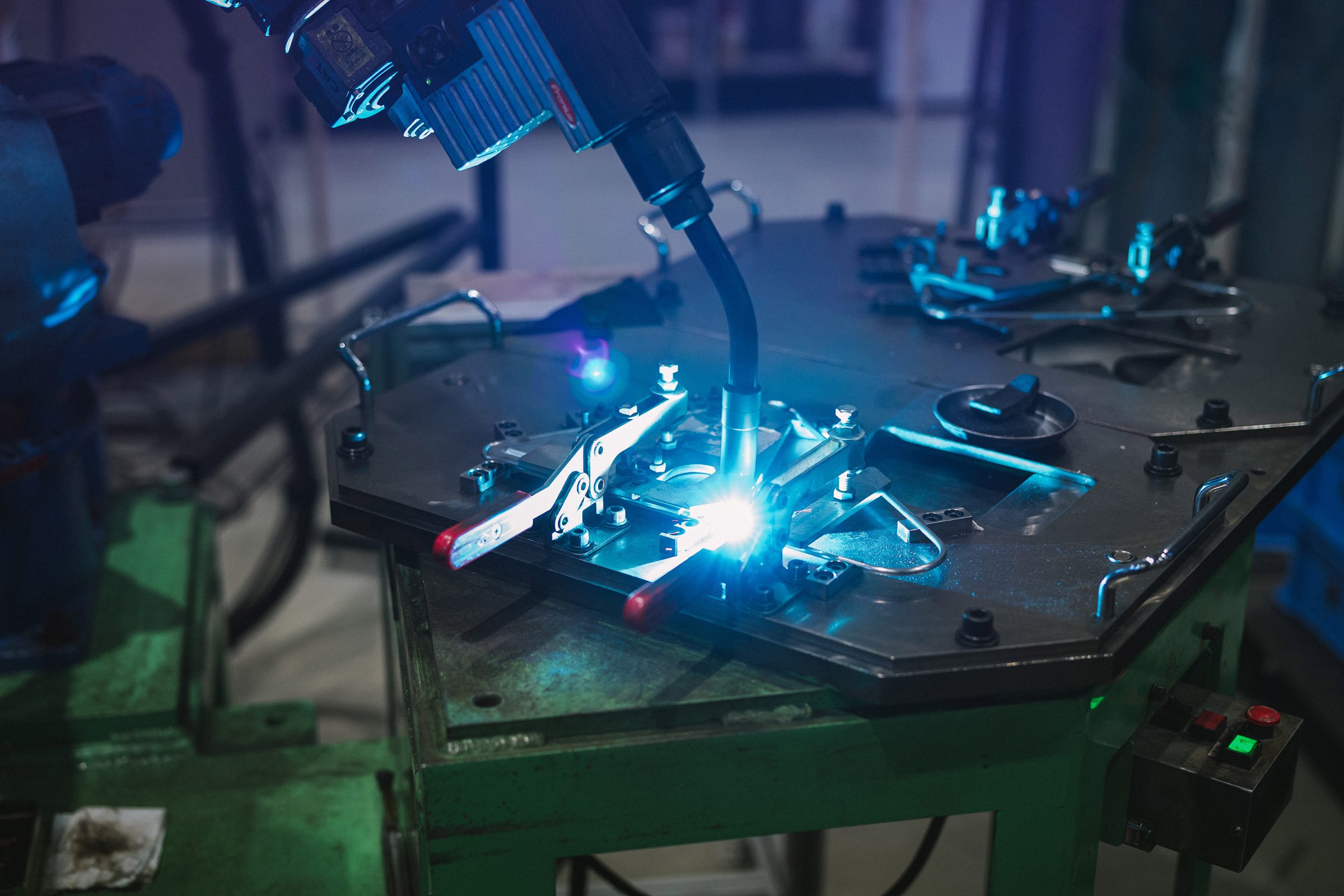
「まずはステンレス板の表面に傷がないかを確認します。この時、ロボットの動きを止めないよう、瞬時に見極める必要があります。傷を見逃して次の工程に進めるとそれだけロスが増えますので、このチェックはとても重要です」と話すのは、溶接を行っていたスタッフの佐藤。
溶接を行うのはロボットですが、安定した品質の溶接を行うのには、スタッフにも相応の経験が必要だそうです。
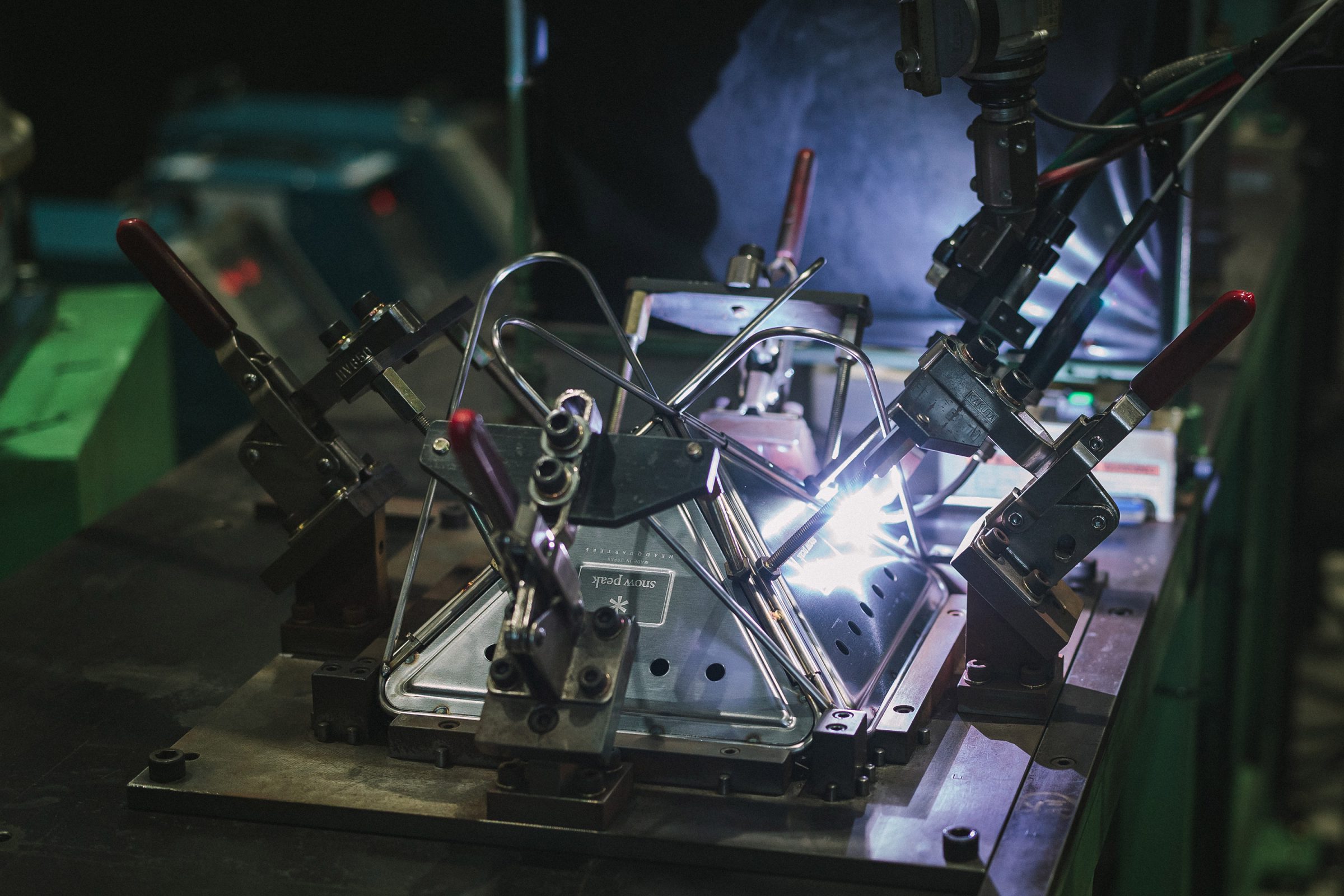
パーツを4枚組み合わせることで焚火台の形になる。
Step 4
4つのパーツを溶接し、完成。
パイプとステンレス板が接合されたら、次の工程でそのパーツを4つ集めて溶接します。治具という台にパーツを4枚セットしたらロボット溶接機の出番です。
「このロボットの溶接には、いくつものプログラムが登録されていて滑らかな動きをします。プログラム通りに正確に溶接を行えるのがロボット溶接機の特長。ですが、実は金属って、反りがあったり生き物のようにばらつきがあるものなんです。だから、ロボットで溶接をした後は必ず人の目で一つ一つチェックをし、修正をしていきます」と小林。

職人の目で確認し、こまかな修正を行う。
すべてを機械に任せて、人はそのサポートに徹するのではなく、機械と人、両者の強みを組み合わせることで高品質な製品を生み出していることが分かりました。
「材料の歪みを見極めて最適な溶接をしなければいけません。溶接時に傷をつけないようにすることや傷を見逃さないことはもちろん、スピードも大切です」とスタッフの速水は言います。
こうして丁寧に、注意深くパーツが接合されて、ようやく一台の焚火台が完成します。
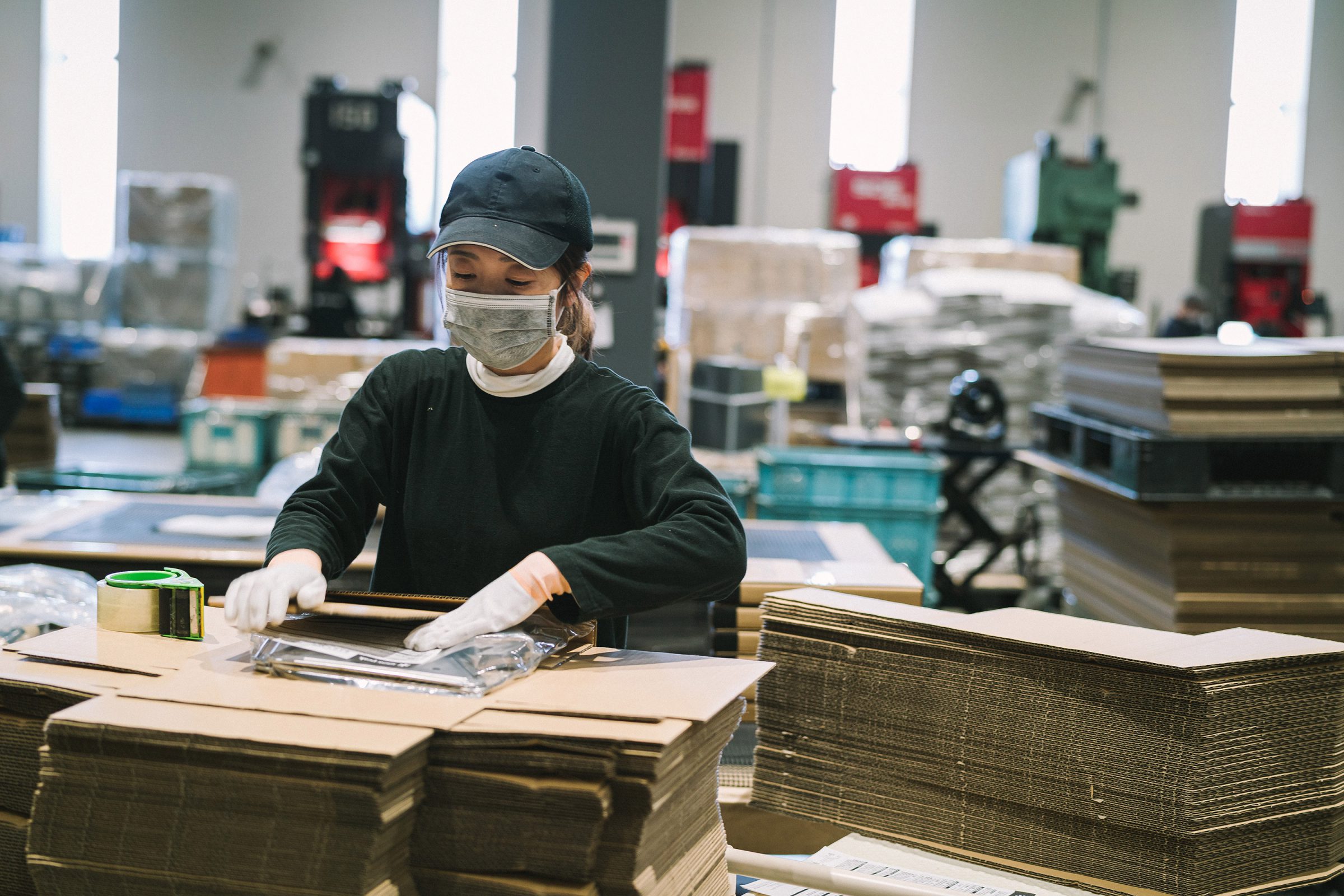
一つ一つ丁寧に梱包し、国内外へと出荷する。
STEP5
検品・梱包、そして出荷へ。
完成した焚火台は、傷がないか、きちんと動作するかを最終確認。その後、袋に入れ、説明書と共に箱に梱包していきます。
「どうすれば、より効率的に作業が進められるかをみんなで考えながら、試行錯誤をしています」と小林。
無駄のない動きで正確に梱包作業が進められていましたが、日頃から細かい改善を繰り返していることを知りました。
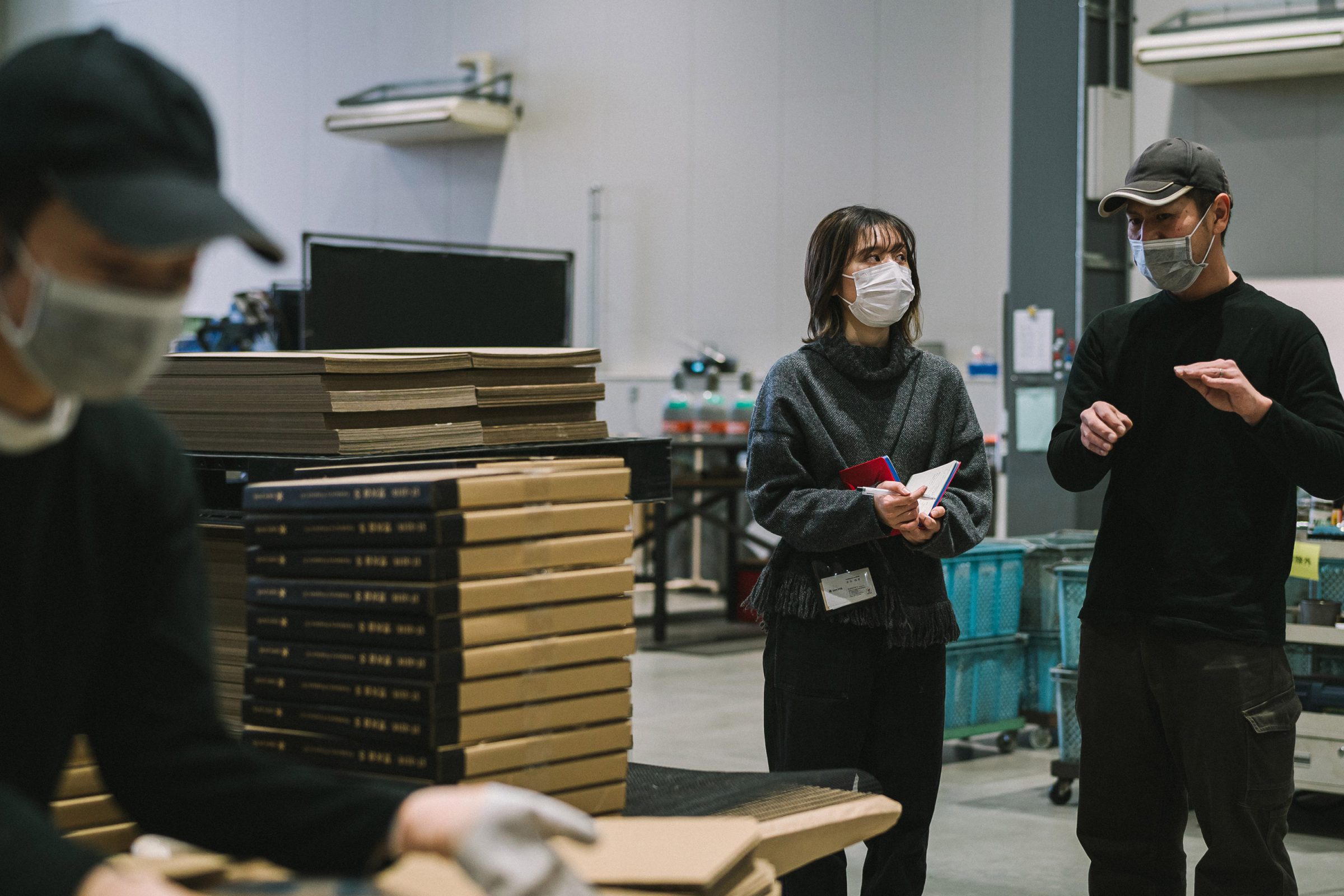
商品を開発するのとともに、そのパッケージや梱包方法を考えるのも、私たち開発部の仕事です。
でも実際に自分が梱包作業を行うわけではないので、今回の取材を機に、どのようなパッケージだと作業がしやすいかを工場で作業される方とコミュニケーションを取りながら考えたいと思いました。
◇見学を終えて。
同じように見える金属でも微妙なバラつきがあり、製造現場ではそれを人の目で見て、手を加えているということを初めて知りました。
そうした職人の技によって、厚いステンレス材はもちろん溶接部分まで頑丈に作られたタフな焚火台が生まれます。スノーピークの焚火台が”一生モノ”といわれる理由は、その点にあると感じました。
良品製造課のみなさんがとても仲が良さそうで、しっかりとコミュニケーションを取りながら連携されているのも印象的でした。
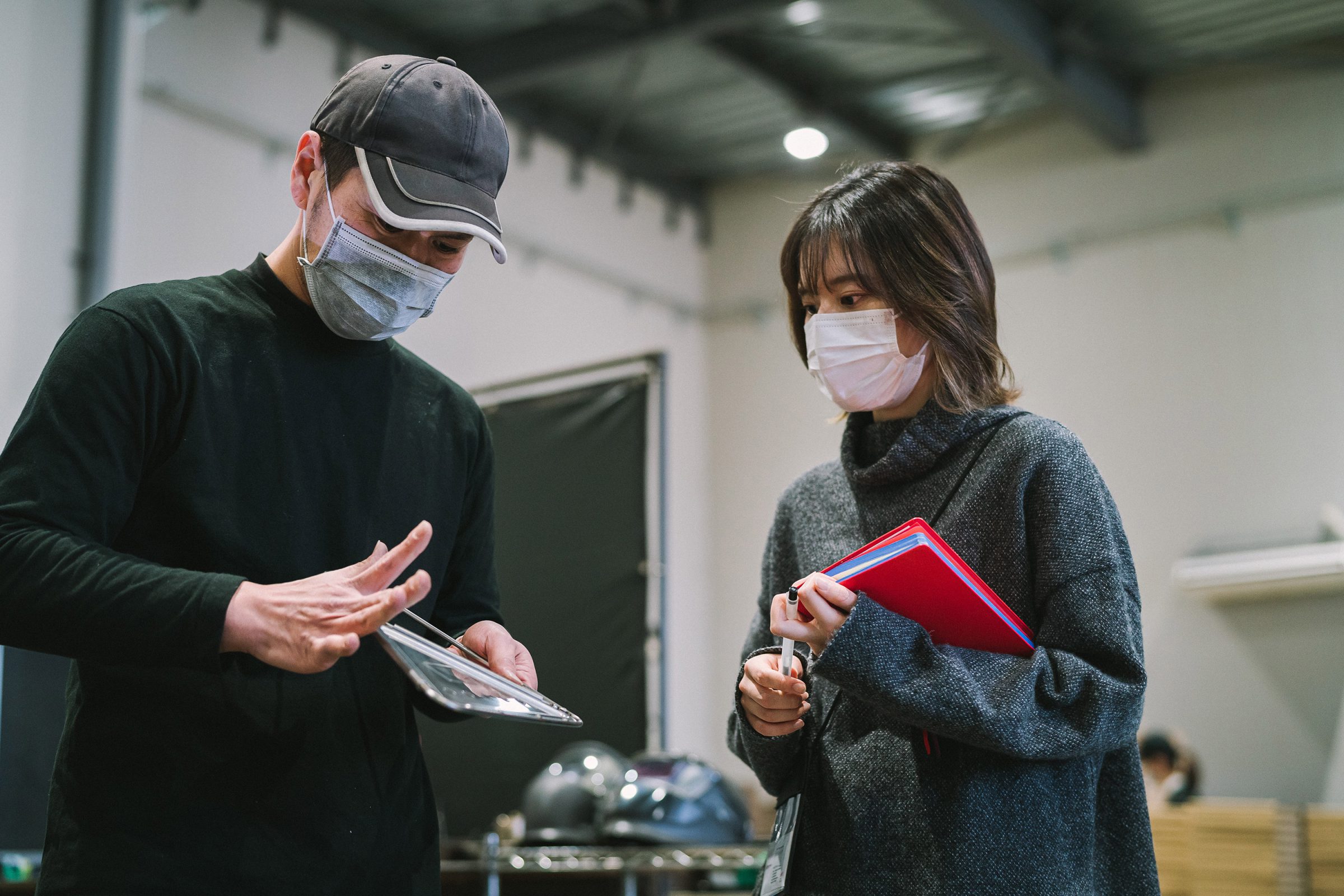
私は製品の開発に関わる一人として、環境への影響が少ないものづくりをしていきたいです。実際に製造する段階でどのような課題があるのかを想像しながら、アイデアを出せるようになりたいと感じました。
今回ご紹介したスノーピークの工場は、雪峰祭などのイベントの際には見学も可能です。ぜひユーザーの皆さんに、実際に製造の様子を見ていただきたいです!
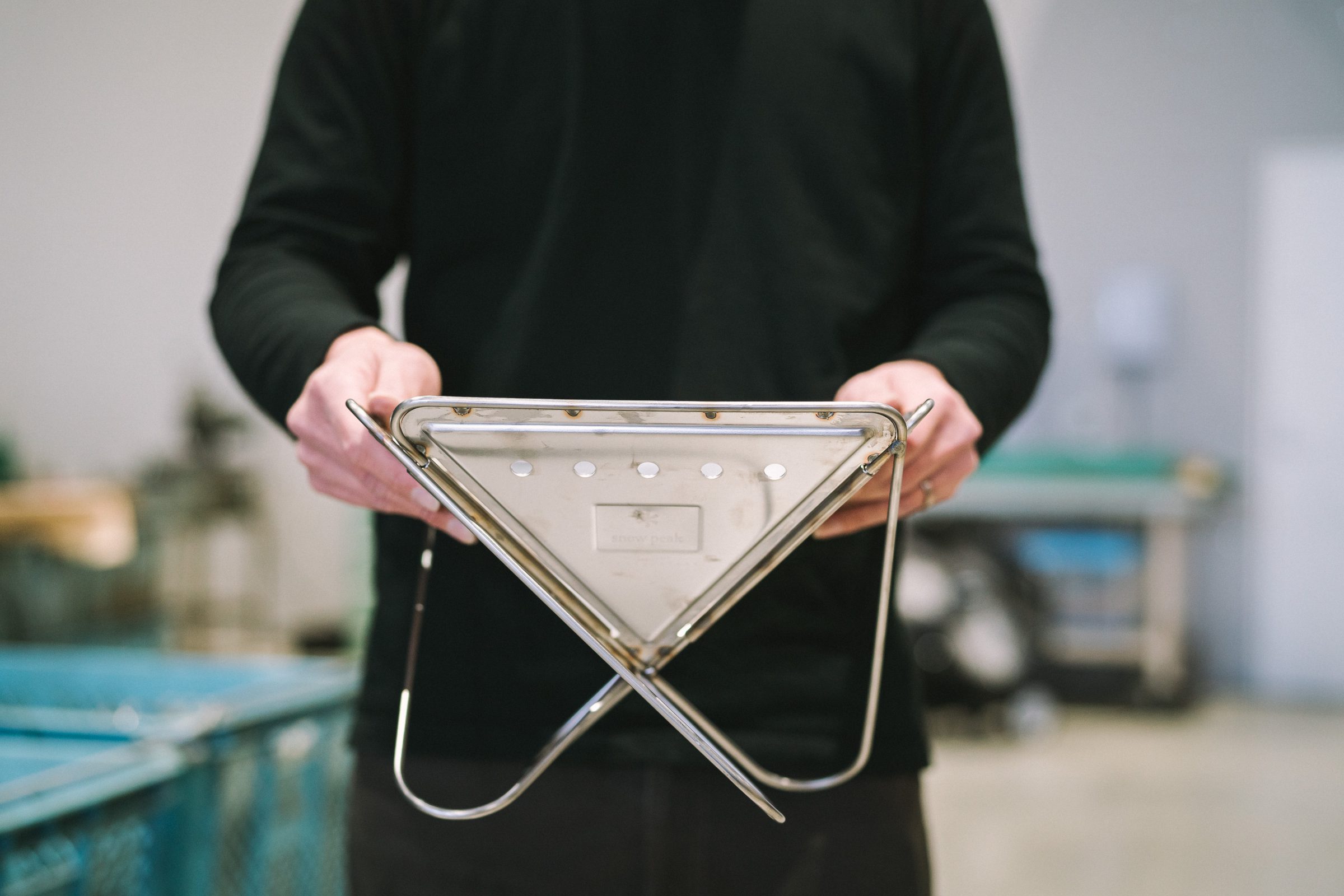
Epilogue
いかがでしたでしょうか。自然は私たちを癒やしてくれますが、穏やかな天候が急変し途端に厳しい面を見せることもあります。
だからこそ、私たちは誰もが安心して快適にアウトドアで過ごせるように、圧倒的な品質を求めて製品づくりを行ってきました。
職人の街・燕三条で生まれたスノーピーク。ものづくりにかける精神はこれからも変えることなく、国内外のパートナーと共に高品質の製品を提供していきます。