【製品】 from STAFF職人を訪ねて vol.1
Experience開発課Shota Aramaki/荒牧 翔太
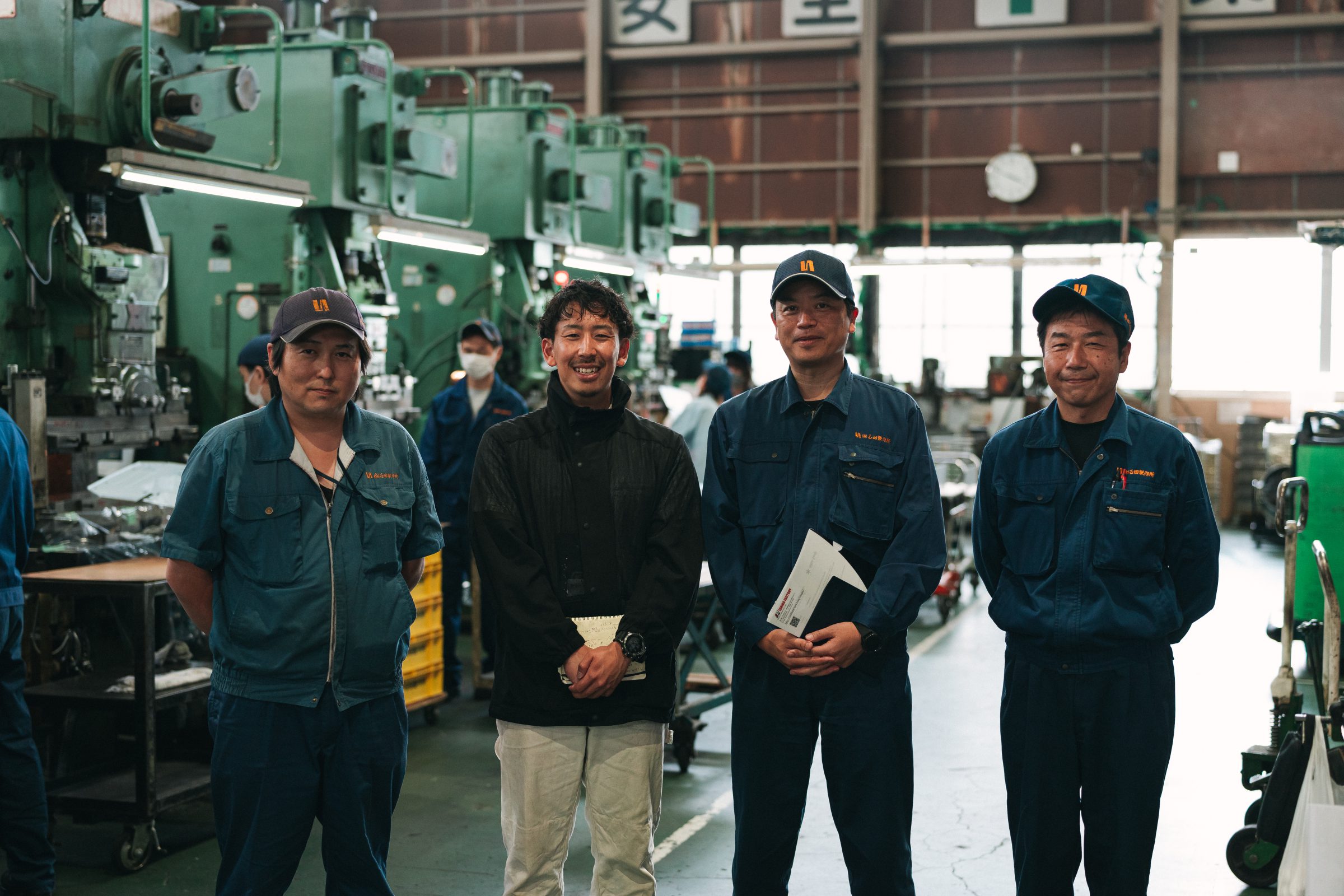
Prologue
新潟・燕三条が誇る金属加工の工場をはじめ、日本はもとより世界各地のパートナー工場でつくられるスノーピーク製品。それらは、機械と職人の知見や技術を組み合わせることで生み出されます。そんな製品群が工場でどのようにつくられているのか? スタッフが詳しくご紹介します。
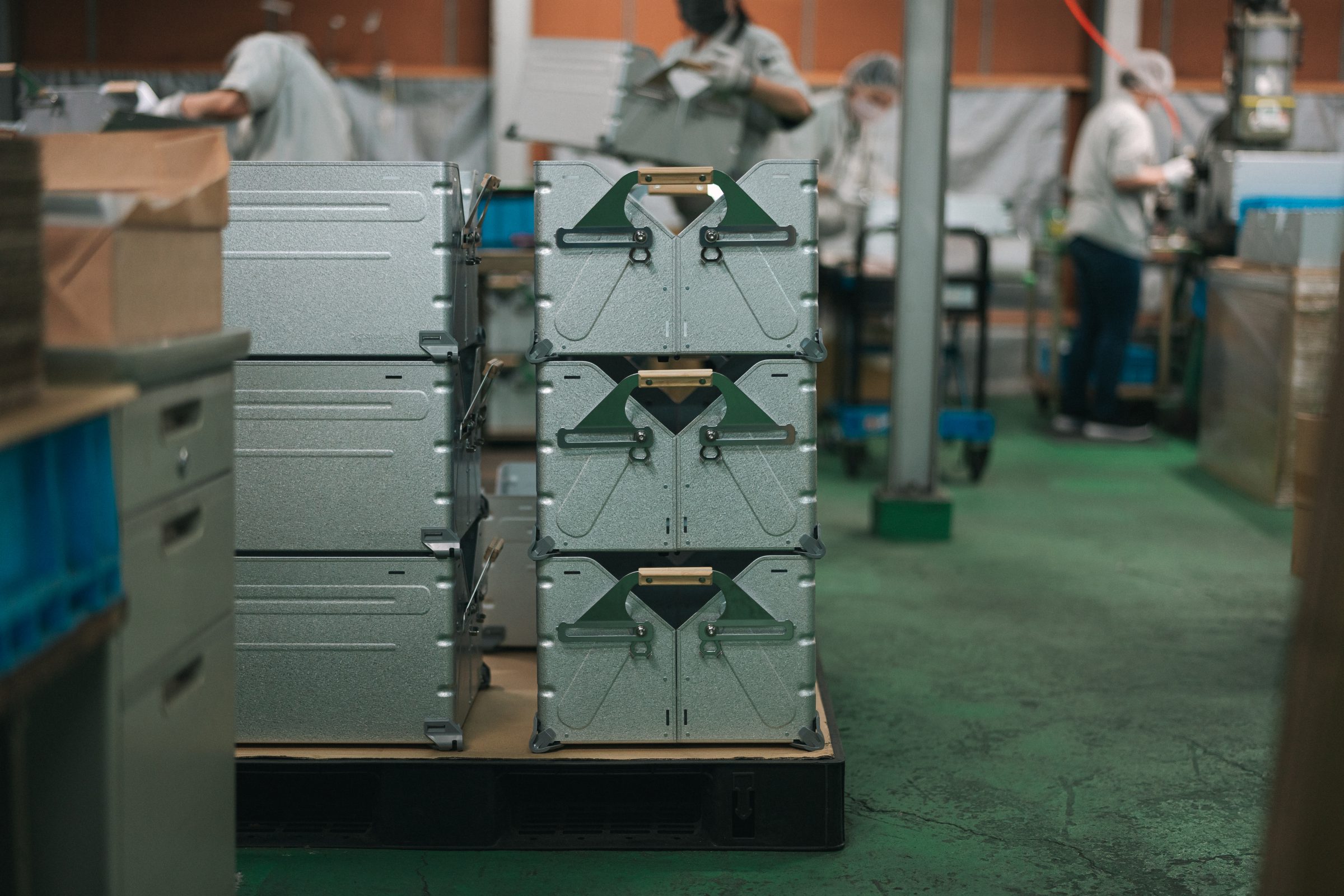
「収納棚を持ち運ぶ」というコンセプトで、2012年に誕生した「シェルフコンテナ」。スノーピークが本社を置く、燕三条地域で製造されています。今回は、日頃からこの製品を愛用しているスタッフの荒牧(Experience開発課)が、その製造の模様を取材しました。
◇1枚のラフスケッチから始まった新製品の開発。
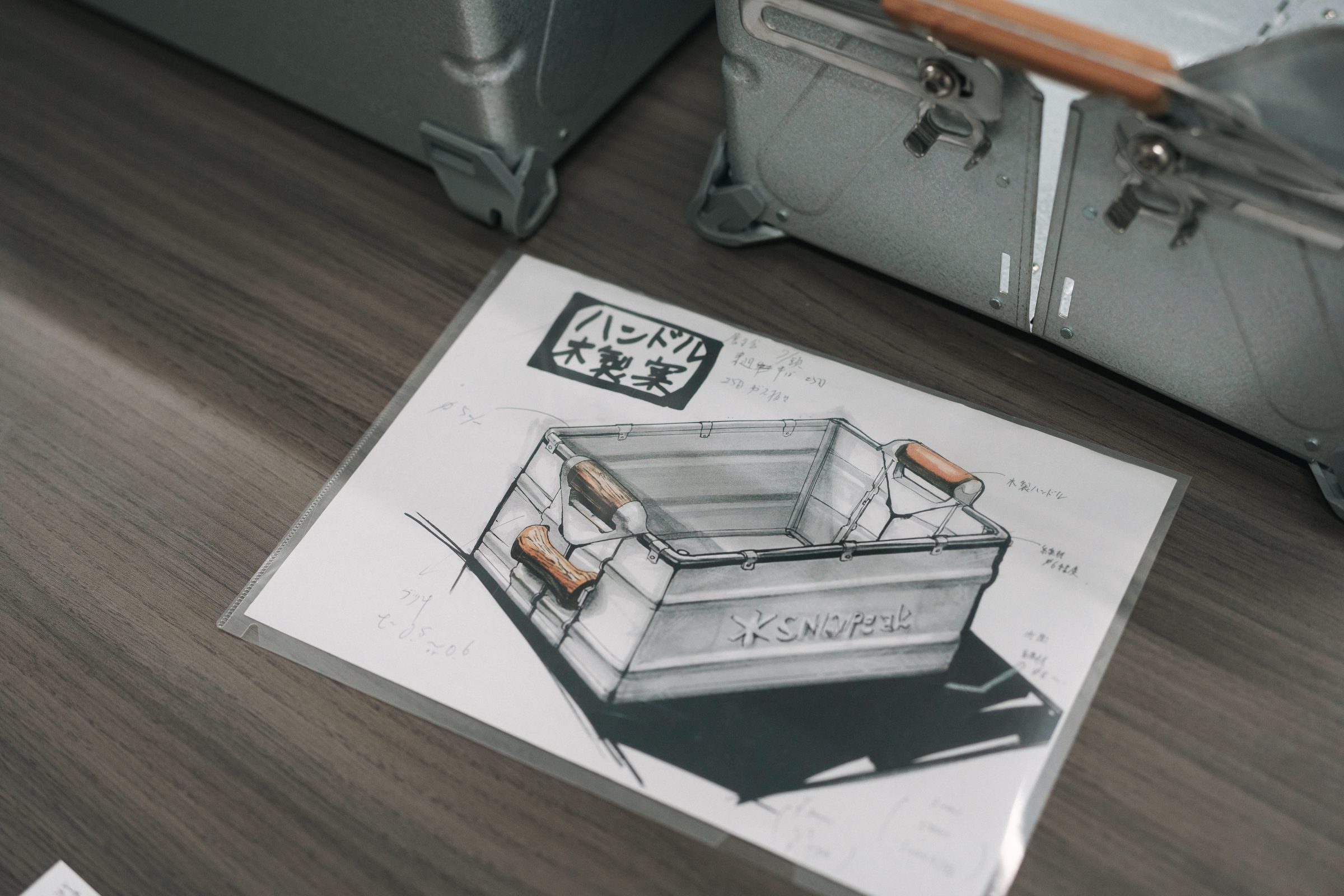
開発者が持参した手書きのラフスケッチ。職人との二人三脚で、現在の製品が形作られた。
シェルフコンテナは、道具を収納する頑丈なコンテナとして使えるだけでなく、特殊な仕掛けによって便利な棚に変身するのが特徴。発売から10年を経た今も人気の製品です。25と50の2サイズがあり、僕は25を3つ、50を2つ、愛用しています。
製造しているのは、三条市にある1949年創業の石田製作所さん。精密板金の加工・溶接・金型製造などを行っている会社で、シェルフコンテナの加工・組立て・梱包まで一貫して生産していただいています。
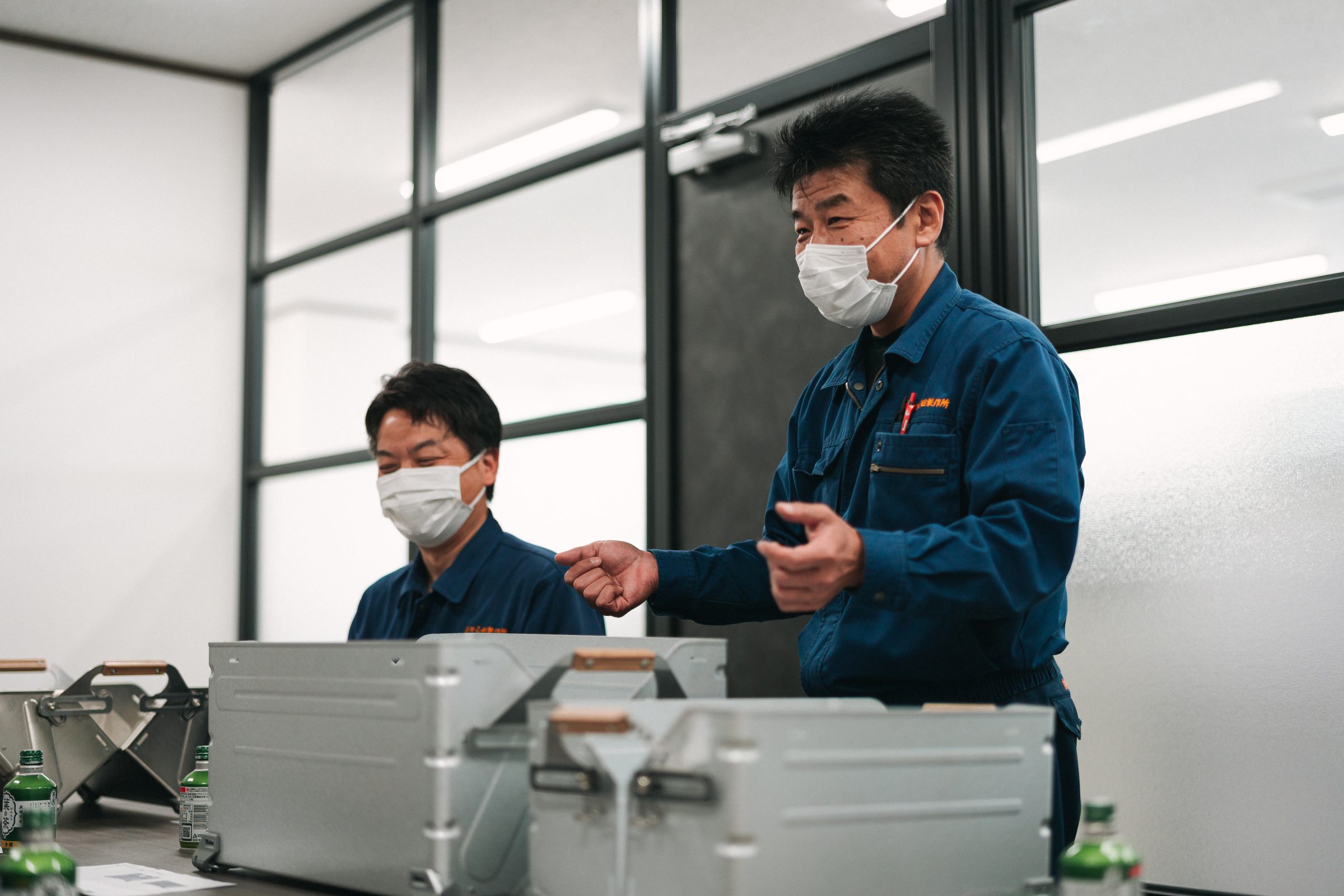
代表の石田さん(写真左)と、常務の鈴木さん(写真右)。
お話を伺ったのは、代表の石田康史さんと、シェルフコンテナの製造の指揮を執ってきた常務の鈴木義篤さんです。
「2011年に開発者さんが『持ち運べる棚を作りたい』と、ラフスケッチを持参されたところから始まりました。『コンテナの箱を開くようにしたい』と言うから、はじめは思わず首を傾げてしまいました(笑)」と鈴木さん。
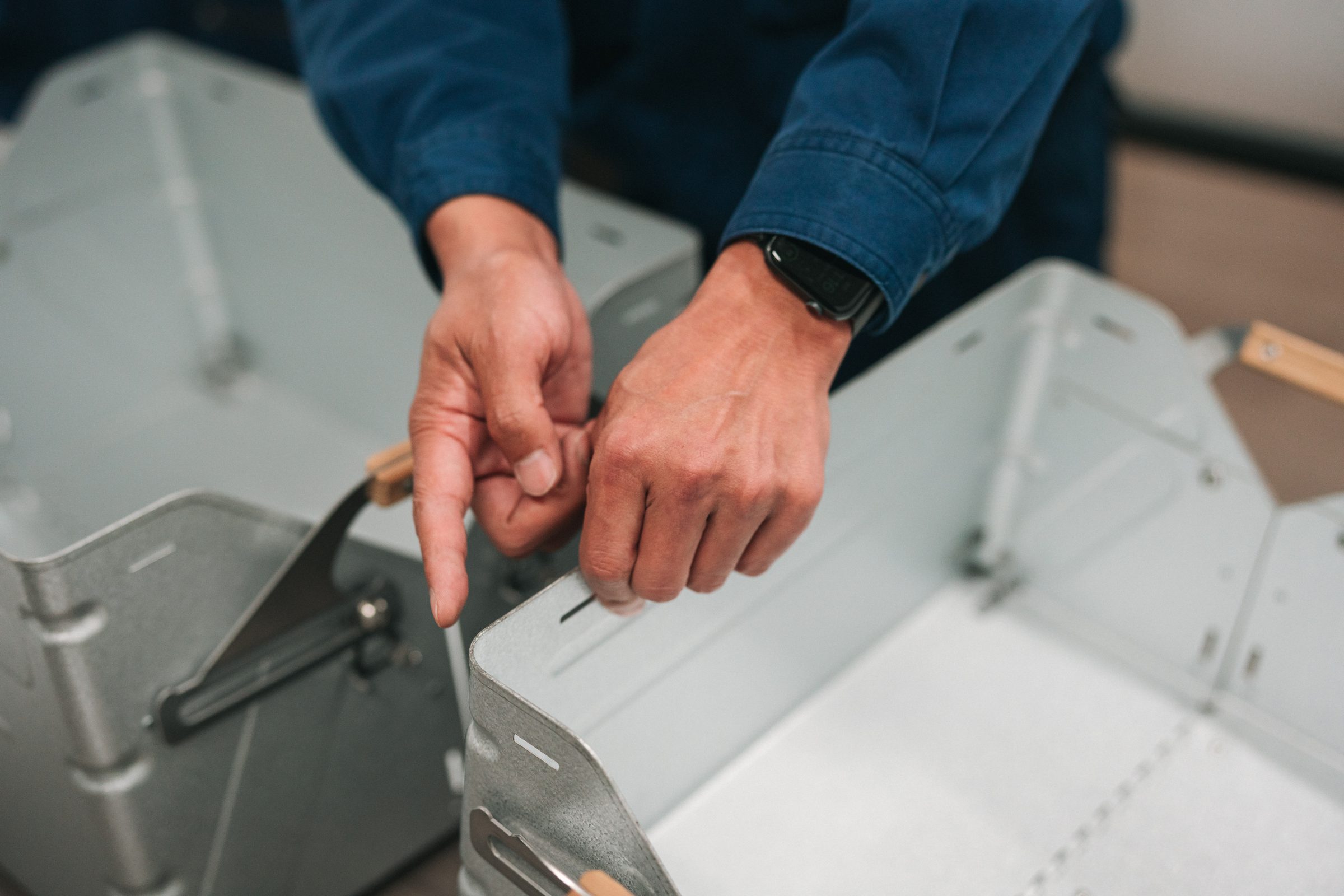
安全のためにふちは「あざ折」という加工が施されている。サイドのカーブする部分も、板金を切らずにそのまま潰したいと開発者がこだわったそう。「金属だまりができやすい部分なので、嫌なこと言うな~と思った(笑)」と鈴木さん。
その後1年半をかけて、素材の選定からロック機構、強度を確保する加工方法に至るまで、何度もやりとりを重ねながら仕様とデザインを決めていったそうです。
「コストバランスや耐久性・質感を考慮した上でガルバリウム鋼板を提案したり、金属板が反らないようにビードやリブという凹凸の最適な入れ方を考えたりと、さまざまな工夫を行いました」と、鈴木さんは当時のこと振り返ります。
◇コロナ禍で需要が急上昇。ロボットとの協働が始まる。
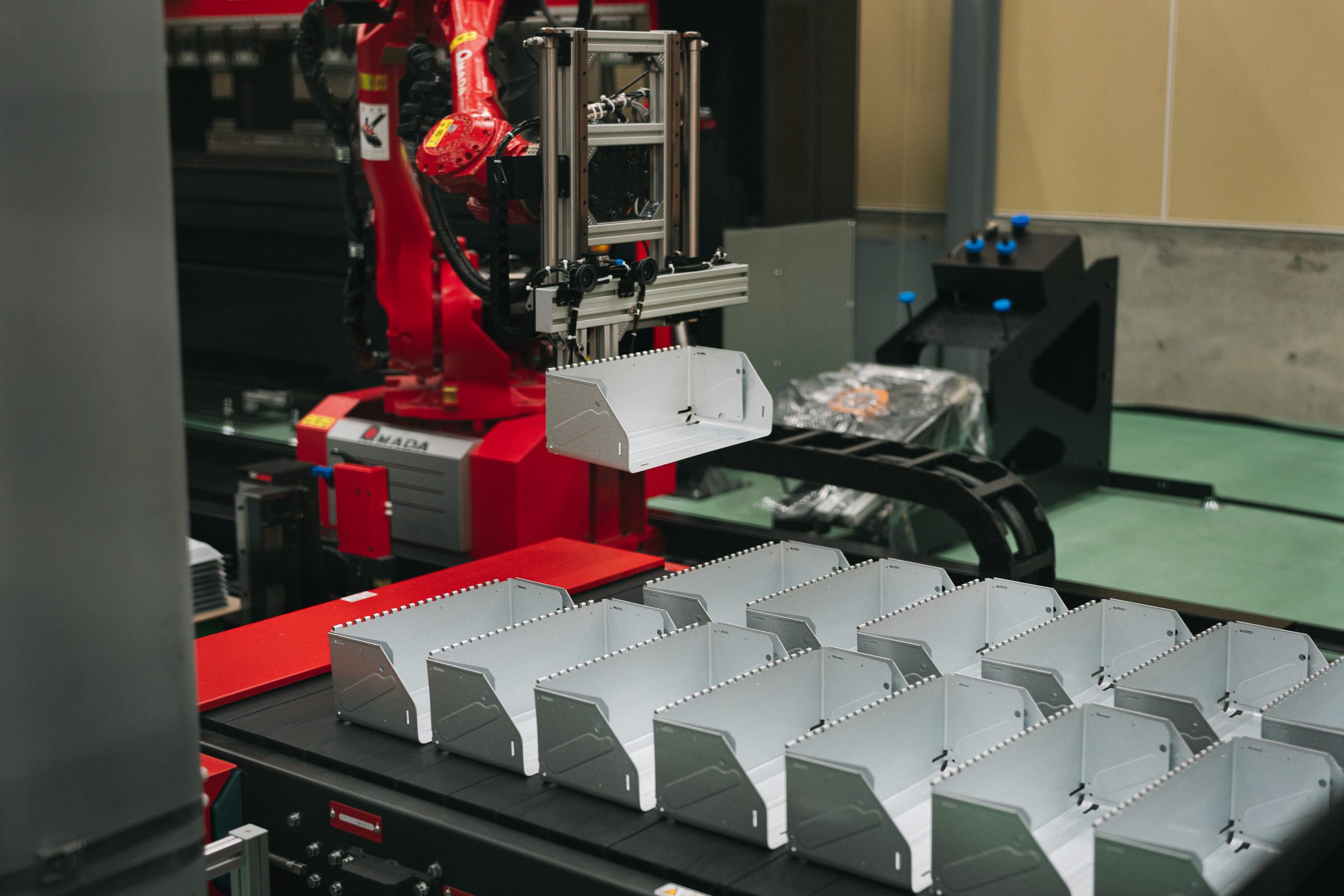
折り加工を施す専用ロボット。2022年から本格稼働した。
「ようやく発売し、初回ロットを生産してから1年間、次の注文が来なくて(笑)。簡単には世に受け入れられないんだな…と思いました。それから3年ほどかけて徐々に注文数が増えていきましたね。
2020年になると当初の想定をはるかに上回るオーダーをいただくようになり、スノーピークさんからは何度も増産の相談を受けました」と、鈴木さんが発売してからのことを教えてくれました。
しかし製品が多くのユーザーに認められ、需要が高まる一方で、石田製作所は大きな決断を迫られることになりました。
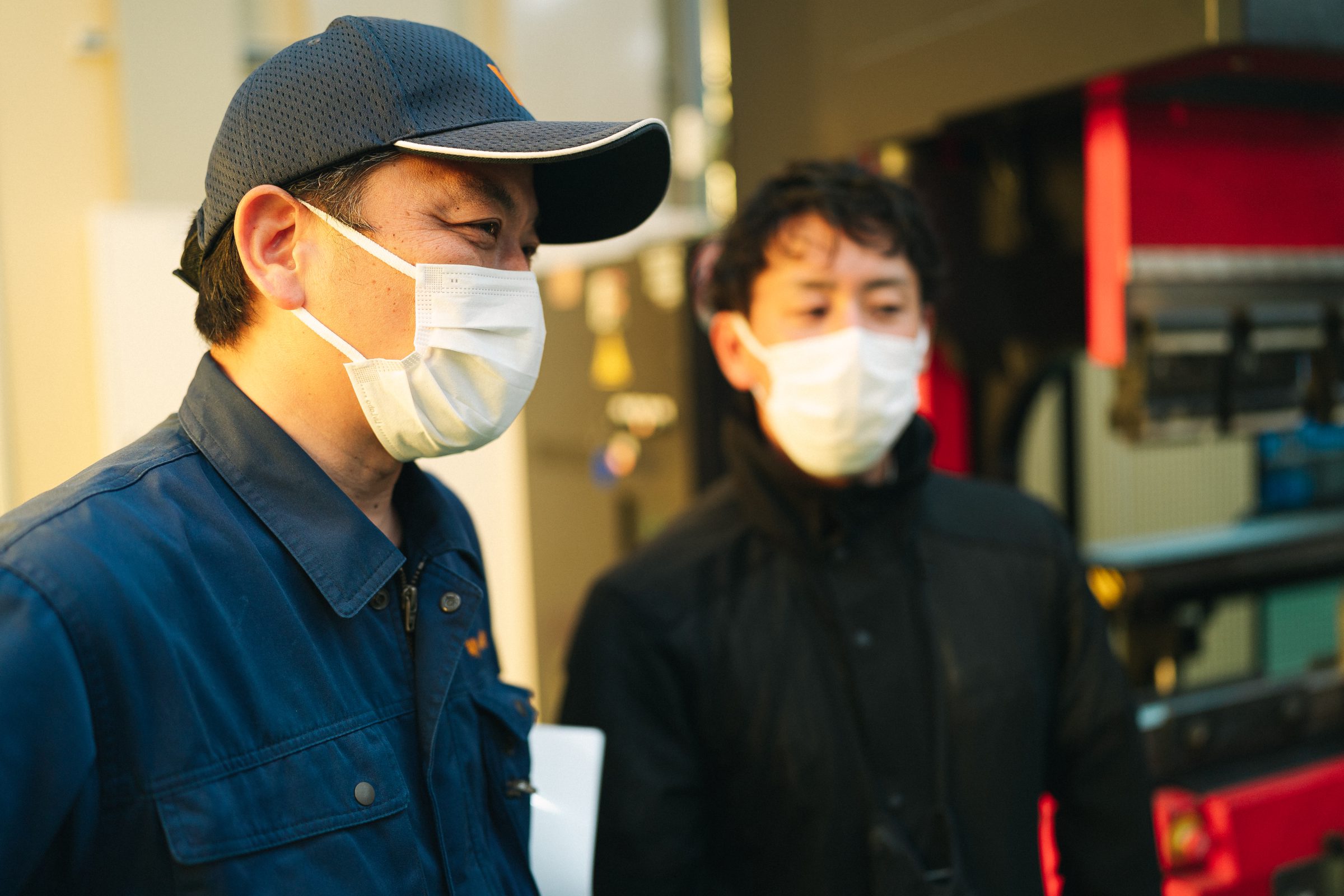
ニーズに最大限応えるため、ロボット導入という大きな設備投資を決意した石田代表。
「増産に次ぐ増産で、現場では職人たちが手作業で朝から晩まで製造にあたり、限界ギリギリ。それでもオーダー数は増え続けました。いよいよ出荷が間に合わなくなり、売り場では品切れが続出してしまったんです…。
そこで工場を新設し、作業の一部の曲げる工程を自動化することにしたんです。前例のない挑戦でしたが、ロボットの導入によって現在は大幅な増産が可能になりました」と、代表の石田さん。
大きな投資をして量産体制を整えるには、相当な覚悟が必要だったのではないかと想像します。そもそも、どこでどうやって作られているのかを知らなかった僕にとっては驚くお話ばかりでした。
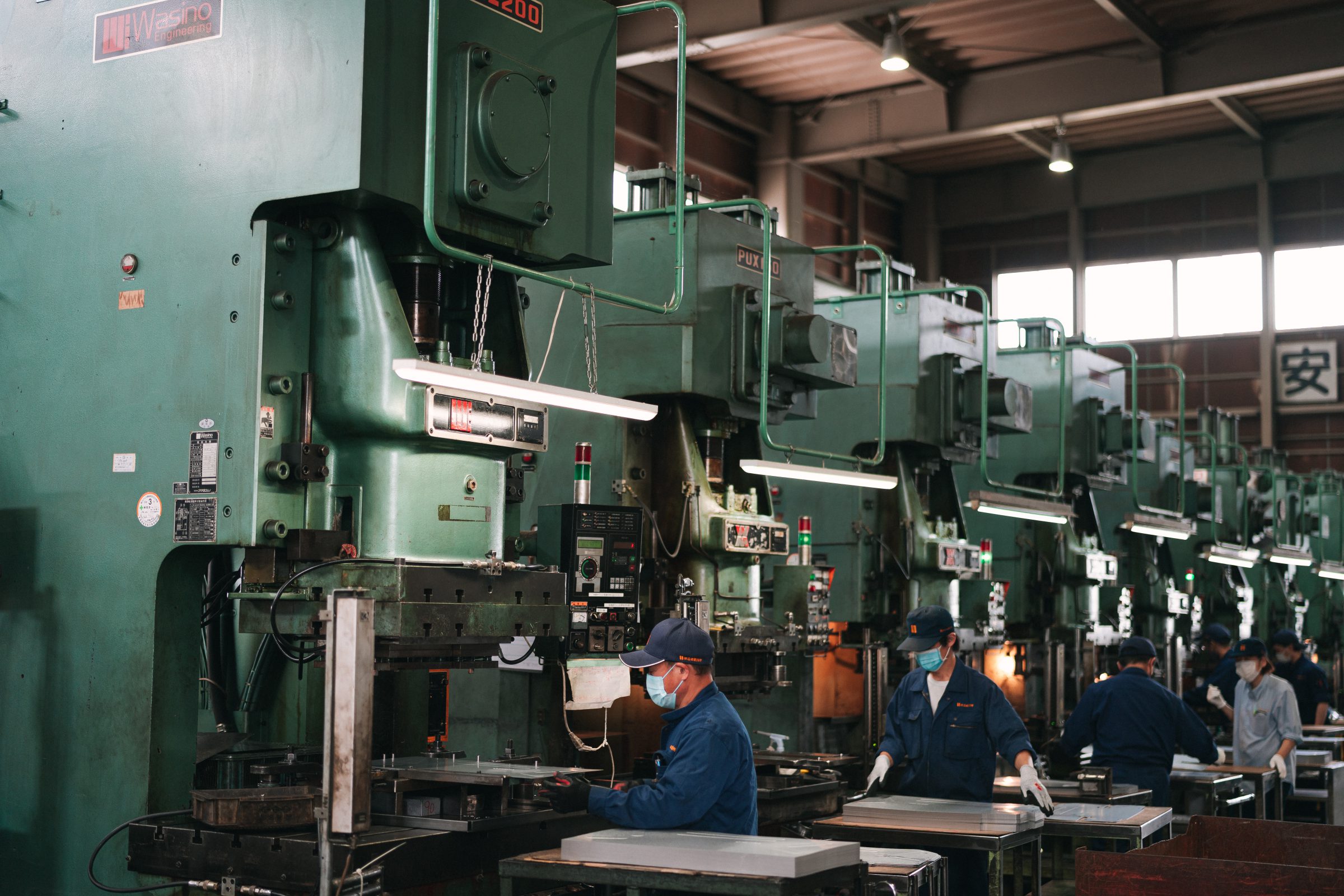
STEP1
板材のプレス加工
開発ストーリーを伺ったところで、いよいよ製造現場へ。
まずは、プレスという大型機械を使い、金属板を加工します。1枚の鉄板から製品が仕上がるまで、とても多くの工程があり、職人たちが材料を手に持ったわずかな時間の中でも傷などのチェックをしています。
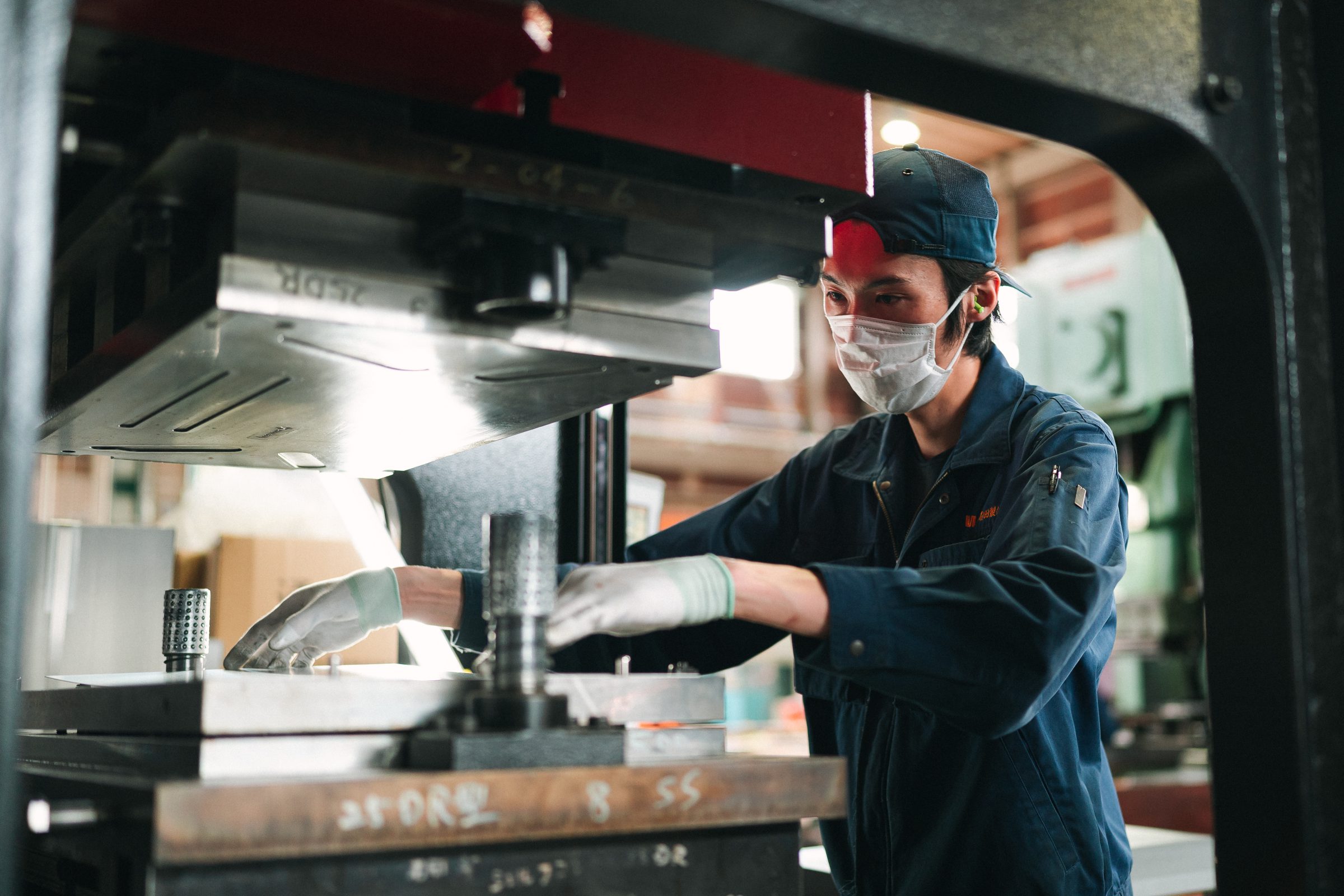
プレスの各工程で、職人たちが厳しくチェックする。
プレスは全部で10工程。開発者と石田製作所さんがこだわったのは、強度を確保しながら面の歪みをなくすことでした。美しさはもちろん、機能面でも重要となるポイントです。
そのために、シェルフコンテナ25と50の側面にはビードと呼ばれる凹凸が施されていますが、よく見ると一部違ったパターンが見られます。表面積の大きい50は歪みが生じやすいため、ビードの一部を二重に。これは鈴木さんのアドバイスによって生まれた仕様なのだそうです。
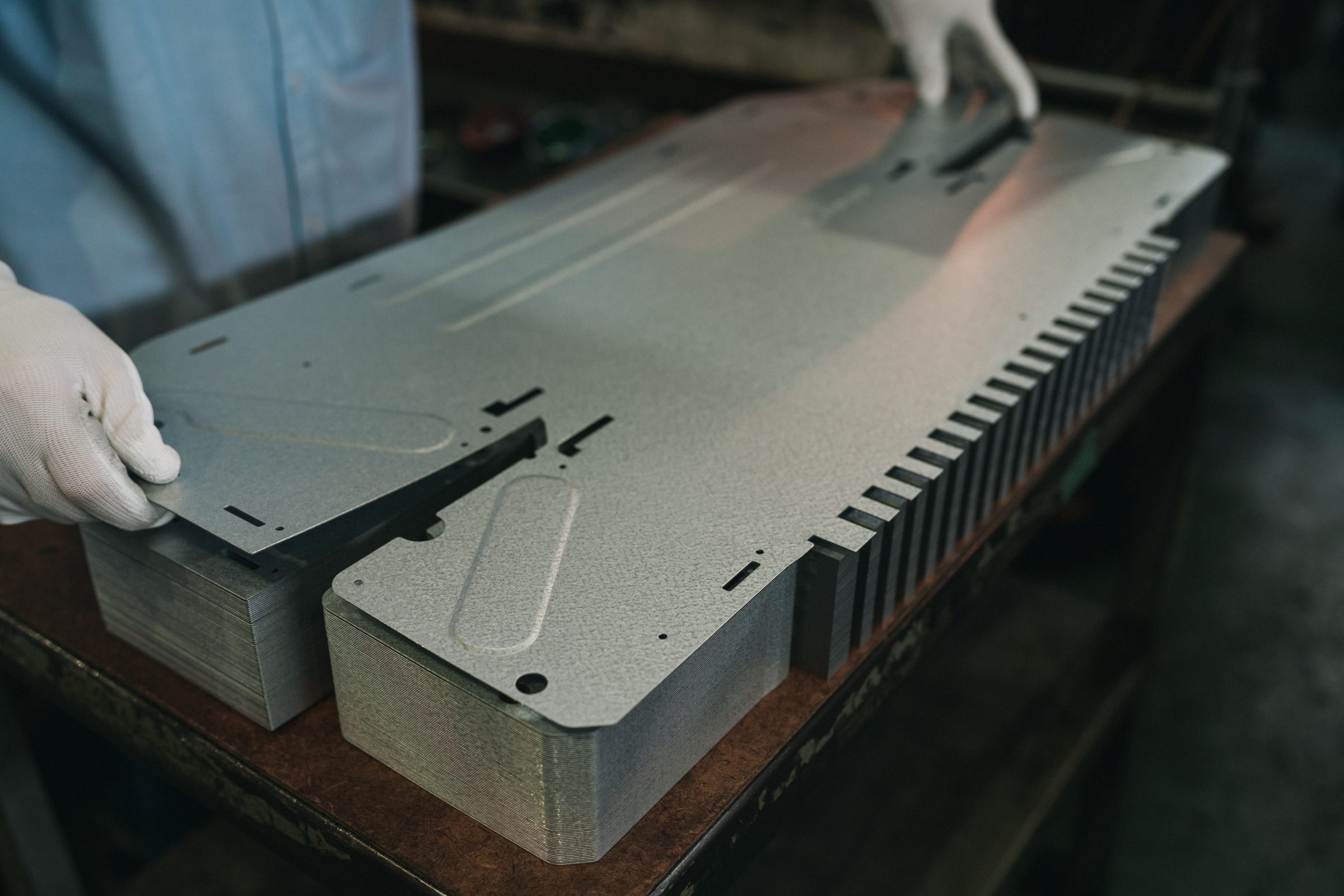
鋼板に施された凸凹が、強度のポイント。
STEP2
ロボットによる曲げ加工と、カシメ・リブ加工
次は、板金の曲げ作業。これまではベンダーという機械を使いつつ、職人の手作業が欠かせませんでした。
2022年から金属加工機械メーカーの「アマダ」による世界初の曲げロボットの稼働がスタート。カメラで対象となる板を読み取り、特殊なアームで吸い上げて5つの曲げ加工を行います。
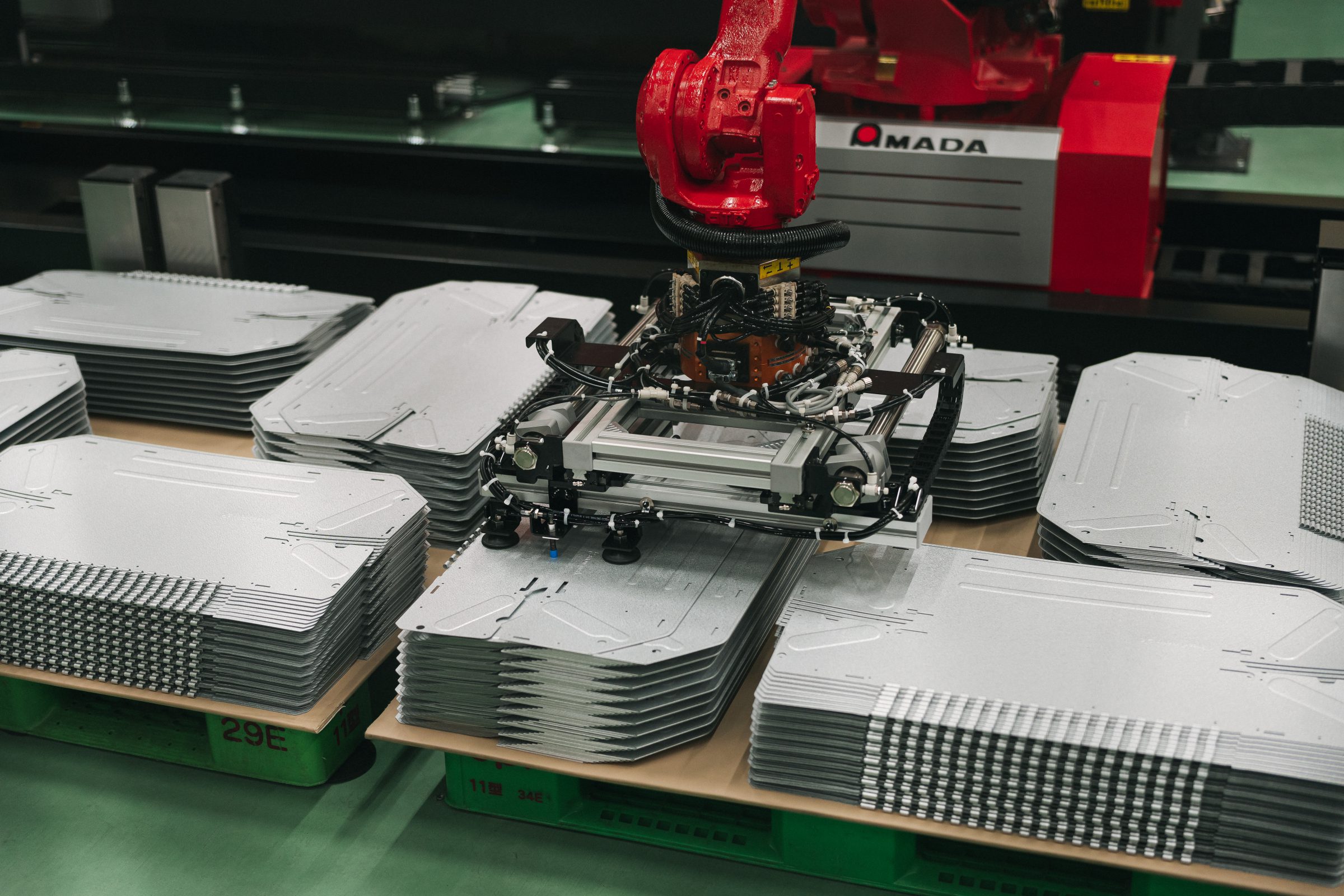
AIロボットが自動で鋼板を検出し、折り加工を行う。
「複雑な形状の製品の曲げ加工を自動化するのは簡単ではなく、アマダさんも最初は難色を示していました。1年程の開発期間を経て、専用ロボットの開発に成功しました。
実際使ってみるとロボットのほうが確実で、クオリティを保って製造し続けられることを実感しました」と鈴木さん。今はロボットを活用した、さらに効率のいい量産方法を職人と模索しているそうです。
曲げ加工が終わった後に、職人たちがカシメ機で板同士を固定し、最後にコーナーにリブ加工を施してさらに強度を高めていきます。
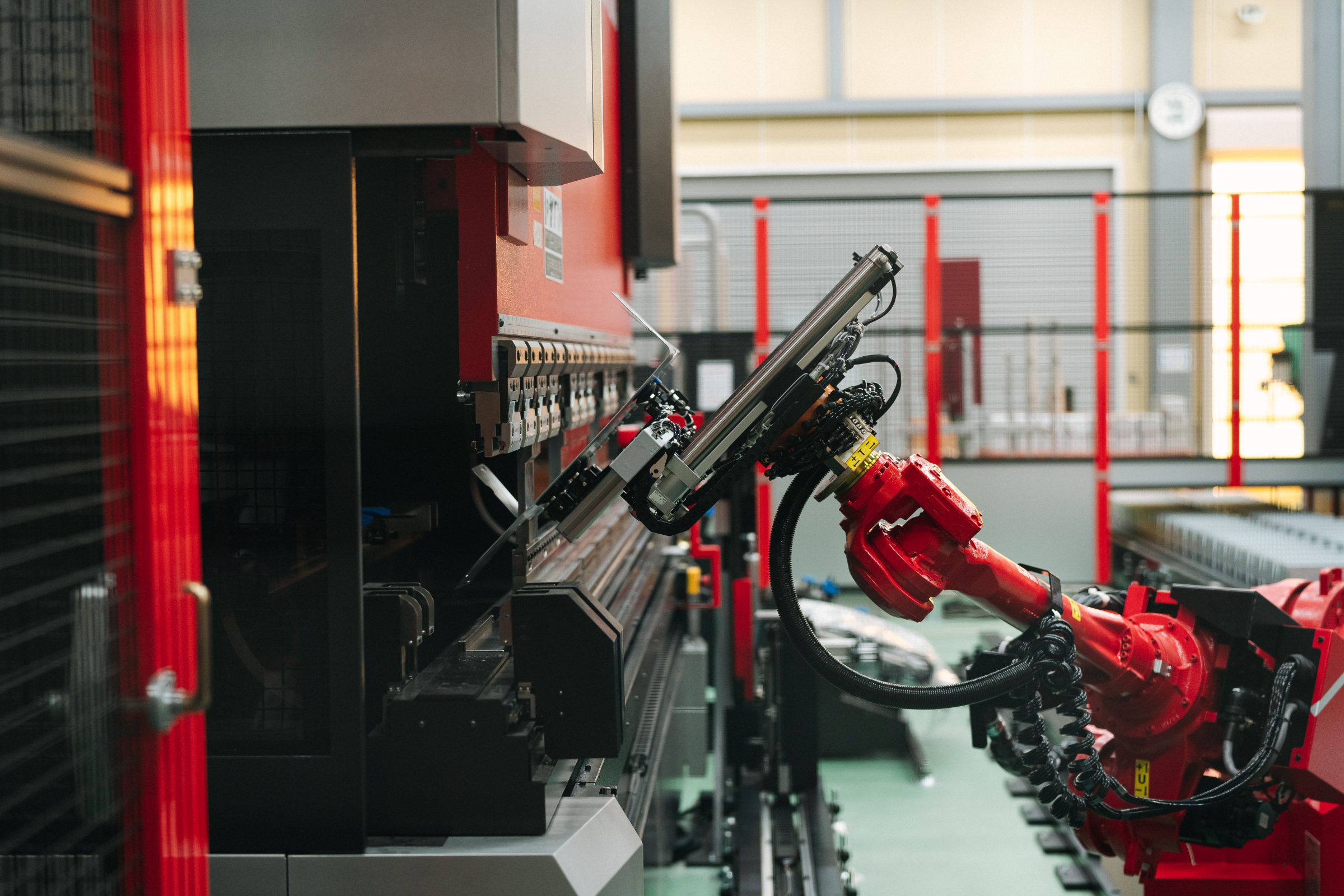
AIロボットの細かなプログラミングは、職人が一から行った。
僕にはスノーピークのものづくりにロボットを使うというイメージがなかったんですが、この導入によってクオリティと生産効率を高めているというのは、発見でした。
職人がロボットの使い方を考えて生産性を向上させているのも印象的で、製造を熟知した職人がいるから生まれたロボットなのだと感じました。

STEP3
組立て・梱包
製造の最終工程である組立て・梱包は、8名で行っています。実はこの作業場は、僕の自宅のすぐ近く。こんなに生活に身近な場所で作っていたなんて、とても驚きました。
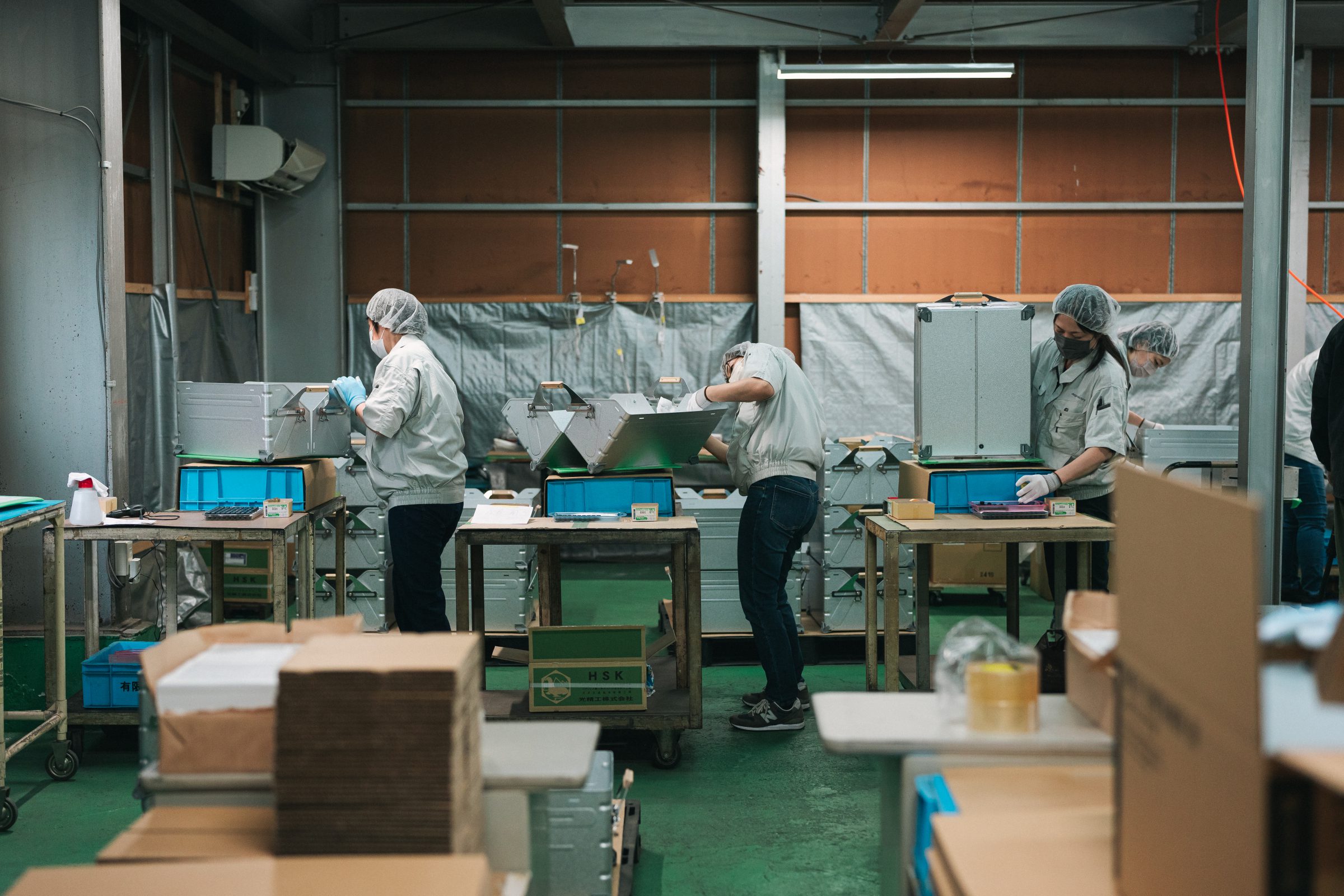
最終仕上げは人間の手で。必要なすべての道具が無駄なく効率的に作業できるように配置されている。
ポップナットを取り付け、その後にコンテナの2つのパーツをシャフトで繋ぎ、ハンドルを取り付けます。
その後、脚部分のパーツを取り付け、最終検査を行い梱包します。最終検査を担当されている方は、素人目では分からないわずかな傷を瞬時に見つけられるくらい目が肥えているそうです。
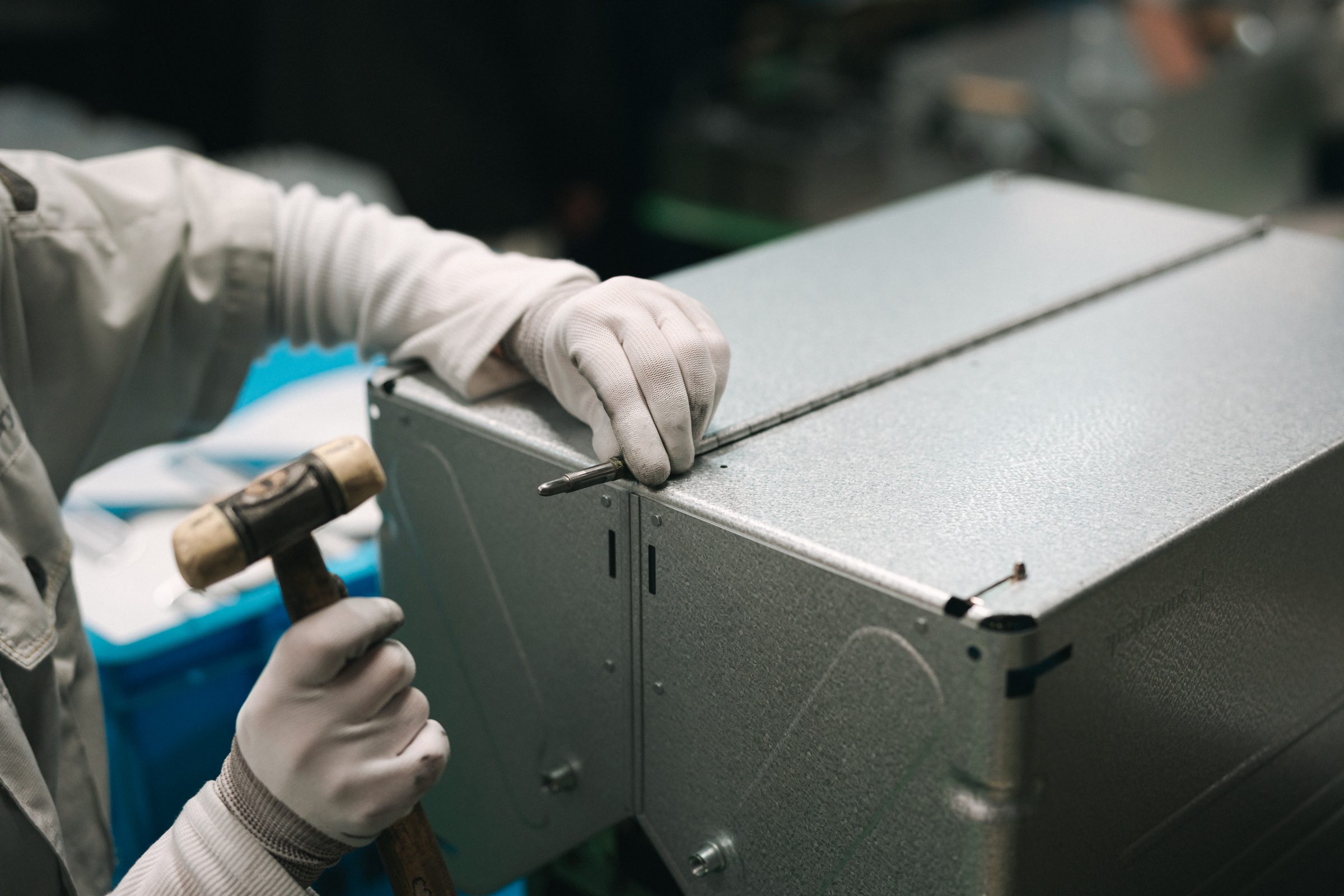
作業の正確さとすばやさは、石田さんや鈴木さんもうなるほど。
「最終検査だけでなく、加工中も工程検査を行います。『検査とは、検査担当者がするのではなく、作っている人が検査するもの』という心構えをスタッフみんなが持っています。製造に関わる全員が検査員とも言えますね」と、石田さんは教えてくださいました。
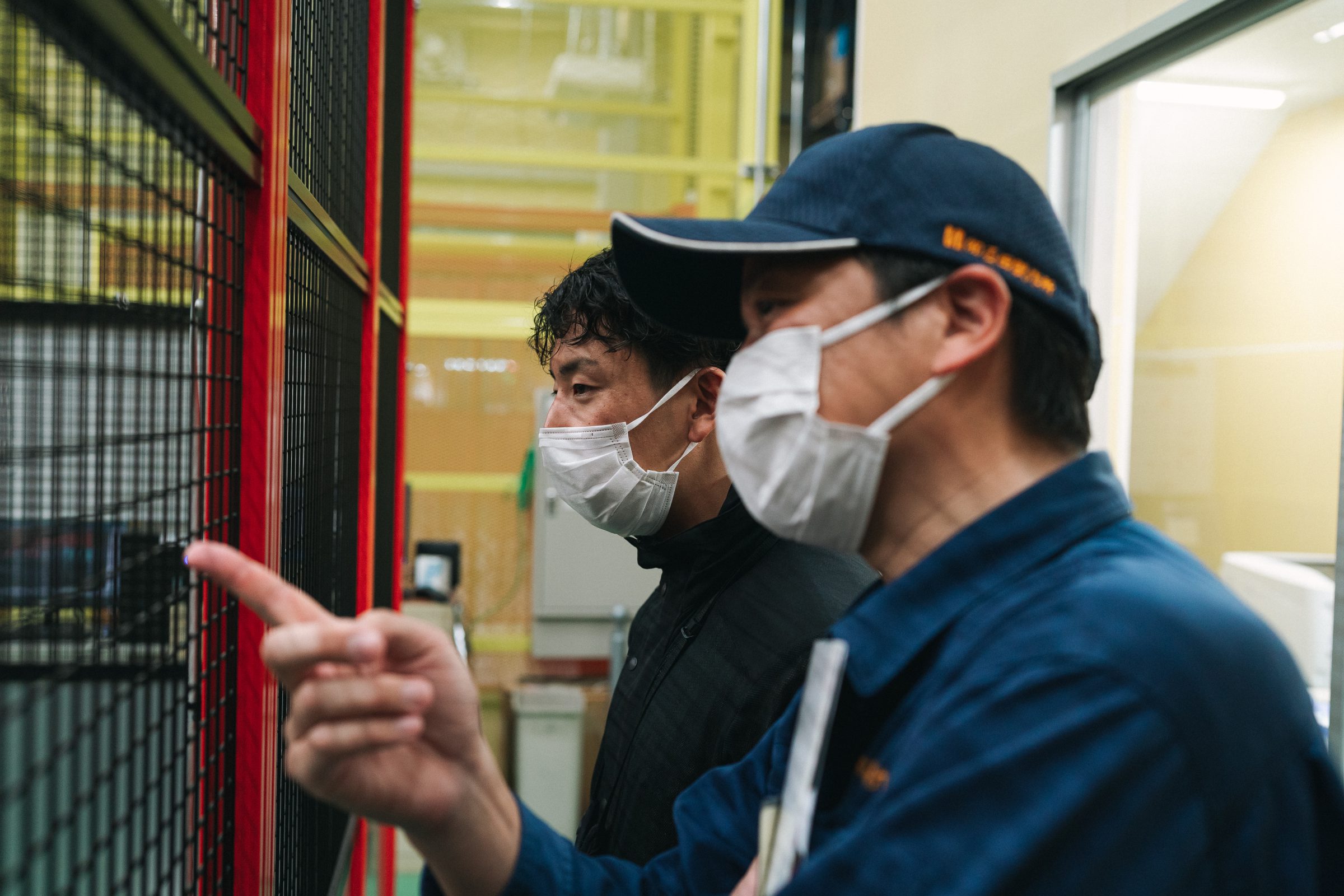
◇見学を終えて。
僕は今回、初めてものづくりの現場を訪れました。ここで見聞きしたことは、僕の想像をはるかに超えていたように感じます。
地域の人と開発者が手を取り合い、世の中にまだないものを突き詰めていく。いろんな人と議論して時間と熱量を込めて作ったスノーピークの製品からは、機能だけではない価値が感じられます。開発や製造のことを知り、シェルフコンテナは燕三条でなければ生まれなかった製品だと改めて思いました。
僕は今、体験開発の仕事に携わっているので、いずれ工場ツアーを企画して、ユーザーさんたちにもこの感動を体験していただける機会をつくりたいです。
また、この記事を読んでくださった方に、ぜひ店頭でシェルフコンテナを手に取っていただき、この製品に込められた「想い」と「こだわり」を感じていただけたらうれしいです。
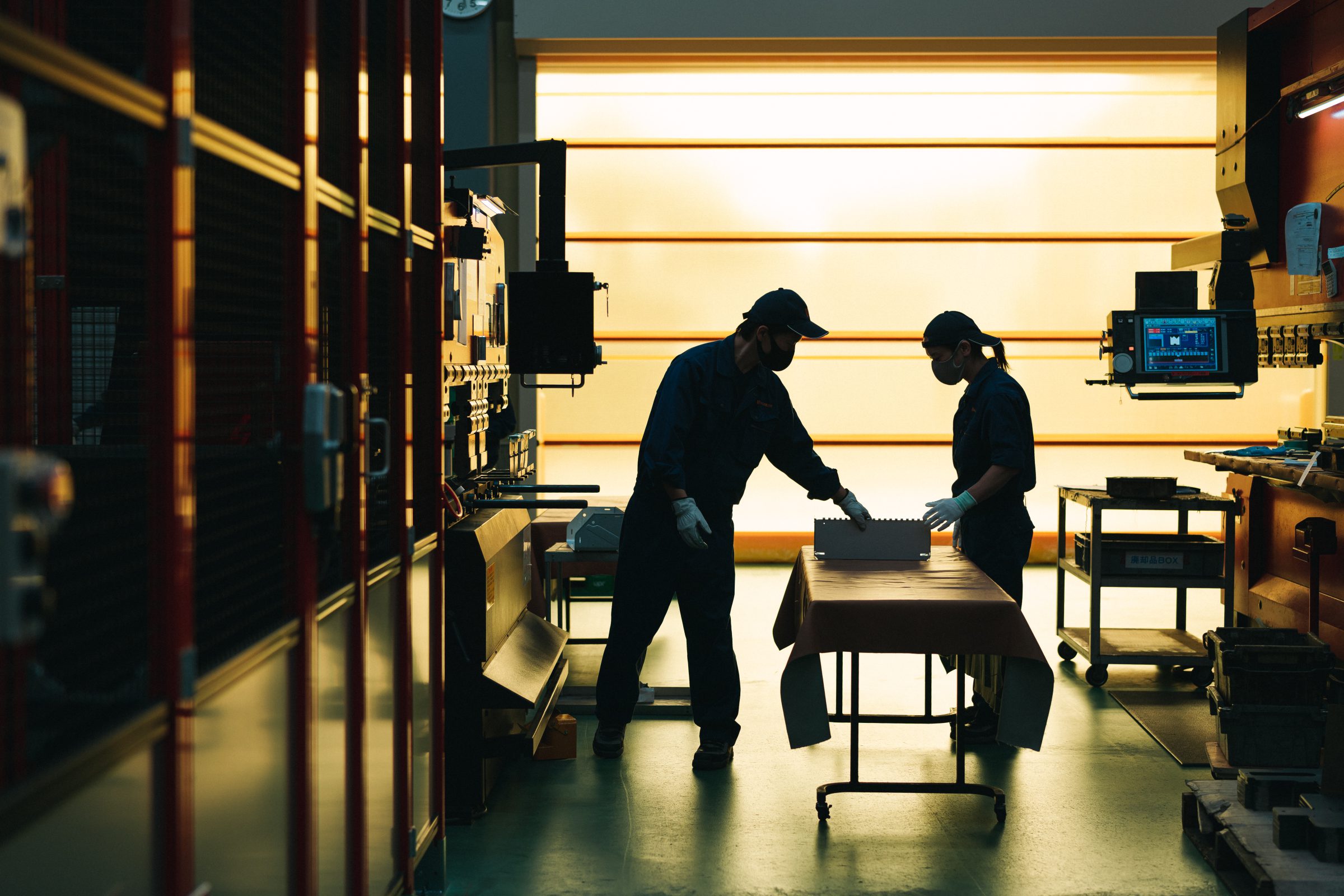
Epilogue
いかがでしたでしょうか。自然は私たちを癒やしてくれますが、穏やかな天候が急変し途端に厳しい面を見せることもあります。だからこそ、私たちはアウトドアで安心して快適に過ごせるように、圧倒的な品質を求めて製品づくりを行ってきました。
職人の街・燕三条で生まれたスノーピーク。ものづくりにかける精神はこれからも変わることなく、国内外のパートナーと共に高品質の製品を提供していきます。